
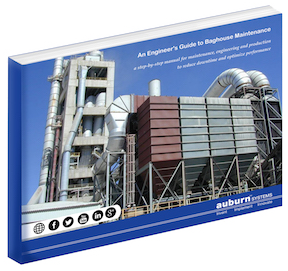
Fluctuation in temperature can cause condensation and moisture problems if allowed to drop below the dew point and must be closely watched.
Give us a call at 410-822-6900 or send email to problem.solved@caloris.com to be connected with a spray dryer specialist. Hoppers to see that they are being emptied.
One of the facilities exhibited both reduced pressure drop and increased bag life as a result of the modification. Access important shareholder information. The clean air side of the collector must be kept clean. This can be avoided by purging the collector with warm dry air prior to startup and after shutdown, keeping the collector above the dew point, with pre-heaters if necessary, and making sure the collector is insulated.
In addition the client expressed concerns over the inability to operate the systems on a consistent basis due to plugging of the filter elements. Each section of the guide provides concisely written content and includes images to help illustrate the solutions. This troubleshooting guide will show you how. Simple changes can often solve persistent baghouse filtration problems, or help a marginal system become more reliable and efficient. navigator.javaEnabled()==1?EXjv="y":EXjv="n"; In a short period of time moisture can cause premature failure of bags in a dust collector. The guide is available for download at www.ge-energy.com/baghousetroubleshooting. Included in the ETS scope of work was a review of the system design and operational practices and a comparison with current industry experience and accepted designs and practices. Baghouse Troubleshooting - Premature Bag Failure. This maldistribution results in very high localized velocities which rapidly erodes the bags. Visit us at Booth 619 & 621 to learn more on how GORE Filter Bags ensure reliable, continuous compliance with membrane-based filter technology proven to increase airflow and productivity in the cement plants.
Filter bag fabric are the emissions going through or around the bag ? Our fee-based Technical Material has become packed and won't flow, 1. A subsequent review of the inspection report and information was conducted and a limited number of failed bags were inspected and tested. The modeling also provided valuable input to the baffle design and a level of certainty that the re-design would alleviate the problem. The clients engineering group would then use the preliminary design as a basis for the final detailed system design. Velocity in the duct and the hood face (capture) velocity had to be balanced. Finding solutions in energy, health and home, transportation and finance. 2022 Caloris Engineering, LLC. Its purpose is to capture the product and meet emissions requirements, while allowing your spray dryer to run continuously. GE's dedicated team, leading technology, and global reach and capabilities help the world work more efficiently, reliably, and safely. Check solenoid sub assembly for trash or rust. Fill out our form and we will email you a copy of our Dust Collection Systems Troubleshooting Guide. Shaker mechanisms to insure they are working. If dust contains crystalline particles, it is important to avoid over cleaning.
Document a more detailed procedure for bag and cage packing, shipping, on site handling & storage.
A checklist is provided for quick easy reference as well as a guide for problem solving. Warm collectors must be watched particularly close so that condensation does not form. GE anticipates that plant operators in the cement, rock dust, power generation and process industries will find the guide helpful. pulse, -protect sensing point from dust or water build-up, -incorporate auto-purging system in sensing lines, -if lines are copper, air purge them yearly to release trapped moisture, 3. There are other materials and fabric weights, but this is most common. Visit Gore at the AISTech, the Iron & Steel Technology Conference and Exposition in Pittsburgh, Pennsylvania (Booth 1952). All Rights Reserved.
Learn about governance at GE, including the latest Proxy Statement and information about the GE Board of Directors. Snap band issues- Check out NFMs exclusive SNAPPER CUFF. Powder inside the bag indicates a hole. The reported problems for each system included reduced gas flow at the capture hoods and high differential pressure (dP) across the baghouse.
Explore a timeline of GE technologies that have spurred transformation across the world. On high temperature systems, failure to pre-heat and cool down If it is working well it is only because you keep it so. Improperly timed baghouse cleaning cycles can allow collection of filtrate on filter bag surfaces. possible leaks in hopper.
Establish a cage improvement program with cage manufacturers. Develop a detailed in-house bag and cage specification. The client's design employed both of these considerations at the subject facility. ETS developed several system design options, all of which included revised hooding and ductwork specifications along with all pertinent velocity/volume and static pressure calculations. This task was necessary so that we could have a complete understanding of the nature of each systems problems and the specifics of the hardware involved. "jv="+EXjv+"&j=y&srw="+EXw+"&srb="+EXb+"&",
ClientFood Industry - Granulated SugarDescriptionETS was hired by an international supplier of granulated sugar to evaluate the dust collector systems servicing the granulated packaging and bulk and truck loading operations at the clients facility in the eastern region of the United States. Its that time of the year again! Both system fans were operating at higher than design speeds (rpm). Have your emissions guarantees with your local authorities handy for these discussions. CAUSE THEM, I. There exercises yielded the following conclusions: Both systems were operating at gas velocities that were significantly higher than design values. Here are four mistakes that produce high pressure drops in a baghouse. As a result of the success of this project, ETS was commissioned to address the second problem site, as well as provide bag/cage drawings and fabric specifications for all three locations. A filter bag with a wear strip or bump cuff will prolong bag life by doubling the amount of fabric where the abrasion occurs.
Ask for feedback on how their product will interact with yours. Is the filter bag sealing correctly to the tubesheet? The ETS inspection determined that there was a significant amount of bag to bag contact; probably resulting from tube sheet deflection, bent cages, and imperfect cage installation. The last, but one of the most obvious sources of moisture in a collector, is leaks in the housing. Fast Response, Budget Estimates, Firm Quotes, Additional Information: 800-438-3850 or webinfo@staclean.com, 1. It is further noted that bag to bag contact does not necessarily result in premature bag wear and failure. Discover how our people & technology are solving global issues, improving lives, and changing industries. As a result of this program the client has significantly increase cartridge life thus reducing replacement costs, has a cleaner atmosphere in the process operation area, and is more vigilant in his approach to inspecting and maintaining his system to insure proper operation. Pulsing pressure that is too low can lead to inadequate bag cleaning resulting in blocked airflows and increased energy cost. At GE, we rise to the challenge of building a world that works.
The air volume being handled by the fan, dont guess. Treat your dust collector as you would any other piece of equipment in your plant. The proper method of bag installation and tensioning of bags should be specified by the collector manufacturer to insure the longest possible life.
If you suspect problems with the bag sealing to the tubesheet, investigate the following: If you need assistance diagnosing and correcting baghouse problems in your spray dryer, contact Caloris anytime.
A standard filter bag for a food or dairy spray dryer is often a 16 oz polyester felt. The client had indicated that there was significant bag to bag contact and it was their contention that this was the cause of a higher than expected failure rate.
Whether for your Filter Press, Belt Press, Leaf Filter, Vacuum Filter, or Baghouse, you can count on Micronics deep industry and applications knowledge for the right engineered filtration solution to meet your needs. Please don't hesitate contacting us for your needs! 1. https://www.aist.org/conference-expositions/aistech, Hindalco Awards Contract for Flue Gas Desulphurization (FGD) System to W. L. Gore & Associates, California Supply Chain Act / Human Trafficking Statement. If your bags are charred or melted when they have worked fine before, its likely that build up in the hopper trapped heat and caused operating temperatures to surge. By embracing diverse teams and perspectives, we are better equipped to build a world that works. It will continue passing by the older filter bags in favor of the newer more permeable bags until the overload balanced out the amount of particles embedded within the filter media of each bag, new or old, and equal airflow is reestablished. The best people and the best technologies taking on the toughest challenges. We are back at it again and this time in person, too. Going back to basics, remember that a baghouse is a filter.
There are a number of things that can impact your differential pressure, but before you address these you need to first conduct a bag filter pressure drop measurement so you can identify where in the baghouse the problem is occurring and whether its a filter problem, or a baghouse problem. Usually the maximum operating temperature should not exceed 20% of the rated maximum operating temperature for more than 10 minutes per day.
Bent cages rubbing walls or each other, b. Included in this inspection were gas flow measurements at several points along the duct system. Your email address will not be published. The client expressed concern that each of the dust collectors had experienced premature failure of the cartridges due to silica abrasion. Baghouse compressed air manifold shouldn't drop more than 30% of maximum during pulsing. Baghouse Performance Monitor Expert System. (812) 546-6262 -----COVID-19: Action Filtration is currently in operation. ClientSupplier of the Air Pollution Control SystemDescriptionETS, Inc. was retained by a leading operating equipment manufacturer (OEM) to consult on the issue of potential bag wear at OEM's pulse jet baghouse located at a Midwestern power plant.
Industrial Gas Filtration and Generation Division, Ph: +1 (800) 821-2222 or +1 (816) 356-8400. Partial Change-out, new bags blinded quickly- Many facilities will change only part of their baghouse filters at one time, in an effort to save on maintenance costs. The design change at the second facility, while alleviating the pressure drop concerns, had little positive effect on bag life. For more information, you may want to check out Industrial Gas Cleaning, International Series of Chemical Engineering, Volume 8.
Improper or undersized discharge device, 3. Check your inbox or spam folder to confirm your subscription. We also interviewed key plant personnel and gathered relevant design and operational and maintenance information. There are many coatings and surface finishes available, but often a standard bag will work fine. The problem can occur in collectors operating at ambient as well as elevated temperatures if they contain moisture. If there are carbohydrates or sugars in your product, the air in the baghouse is often at or at least it is near the sticky point, technically the glass transition temperature, of the product.
When baghouse differential pressure falls, you lose efficiency.
Bag life in some sections of this baghouse was less than one month. Baghouse pressure drop effectively means that less air is pushed through your filters, reducing your baghouse capacity and restricting your productivity potential. During shutdown, the guide shows the operator how to purge dirty gases to rapidly cool the baghouse through the dew point zone, minimizing the damage caused by condensation and corrosive salts formed during shutdown.
Proper baghouse protection procedure is that bags are cleaned before shutdown. Explore GEs recent and historic SEC filings.
If it is a money timing issue, consider putting on a blanket order with NFM and releasing/ paying for only part of a set monthly or quarterly leading up to a full change-out. Wet dust cake can seal pores in filtering materials leading to high pressure drops. Voices is a network for GEs US supporters interested in the companys impact in their communities and in issues that impact the company. years of Experience for Dr Dirt Work For You. The client authorized ETS to conduct the flow model, and the results of the study correlated very well with our previous conclusions regarding distribution and failure patterns. A comparison of the actual versus design flow data indicated there were several inconsistencies; in some cases the problems were caused by improper damper settings or ineffective maintenance procedures, while in some instances the problems were caused by poor design practices such as improper location of bucket elevator discharge pick-ups or inadequate hood capture velocity. This is to be used by plant as a reference for future balancing and system maintenance activities. Dust hoods to see that they have not been changed, removed or destroyed. Vacuum Filtration: A Guide to Proper Filtration Equipment Selection to Optimize Your Operation, Micronics Launches Single, Consolidated, Multilingual Website, Stop Leaks in Your Dust Collector & Recover Costs. Micronics Engineered Filtration Group, Inc. Learn more about our culture, businesses, and life at GE. The businesses that comprise GE Energy---GE Power & Water, GE Energy Management and GE Oil & Gas---work together with more than 100,000 global employees and 2010 revenues of $38 billion, to provide integrated product and service solutions in all areas of the energy industry including coal, oil, natural gas and nuclear energy; renewable resources such as water, wind, solar and biogas; as well as other alternative fuels and new grid modernization technologies to meet 21st century energy needs. 1.
Re-entrainment of dust within collector Contact information for general inquiries and feedback.
Keep in mind that what makes a baghouse on a spray dryer unique from other baghouse and nuisance dust collectors, is that inside the baghouse can be a relatively high moisture environment. Hissing sound (possible compressed air leakage), ii. / Quote Request / Trouble Shooting / History / Silo Bin Vents / Trace-It Improper fabric, failure due to incompatibility with gas stream, 2. Use this as a guide, but above all make your own preventative maintenance list. In addition the bags in each dust collector inspected were found to be severely plugged. Moisture in the dust stream often causes dust to stick together and form a thick, wet dust cake.
Access the latest press releases, media contacts, and press tools.
The objective of the evaluation was to inspect the condition of each system, determine system gas volume, balance each system, and make recommendations for system improvement. Check diaphragm valve internals for broken spring, trash, etc. Shrinkage can also occur at elevated temperatures. ETS concluded that the granulated sugar being transported in the ducts posed an unusual problem in that it was a heavy, moist material requiring higher transport velocities than what is typically required for industrial applications. Your gas/ dust pH is among the variables considered to determine the best filter media and fabric construction for your application. The initial task in the ETS effort was to review the design calculations and specifications of the present systems along with any available operation and maintenance records. Explore the latest stories, news, downloads, and press tools. Read GEs 2022 Proxy Statement, vote your shares and access the 2022 Annual Meeting. ClientSpecialty Rock Products ManufacturerDescriptionETS, Inc. was retained to evaluate two separate dust collection systems at the client's facility in West Virginia. concentration)or very fine spherical particles, 1.
The modifications were made and the system has since experienced significantly improved bag life and much lower operating costs.
GE Aviation is a world-leading provider of aircraft engines, systems and avionics. 24012-1309, Florida Office ETS, Inc. 406 W. Crystal Dr.
Learn more about our innovative GORE LOW DRAG Filter Bags, with our improved airflow and meltshop draft which can support the steel industry by meeting the environmental challenges while realizing lower operating costs. The subject baghouse was of long bag design, had a two section cage design, and employed high pressure low volume (HPLV) pulse cleaning. Excessive rust or build-up on hopper walls, 3. Air can enter through cracks in the housing and seams, or around bad seals bringing moisture into the collector. We look forward to working with your team.
In addition ETS was requested to provide preliminary designs and specifications of any recommended system hardware upgrades including belt pickups, dust capture hoods, transfer ducts, main ductwork, baghouses, and fans.
High moisture, moderate heat which can cause hydrolysis, 1.
* How startup and shutdown processes can be improved in the combustion industry, where many plants have only recently converted from electrostatic precipitators to baghouses. Extremely fine dust (less than .5 micron in high We connect capital to infrastructure and deliver innovative financial solutions that help make the world work better. Included in the ETS scope of work was a review of the system design and operational practices and a comparison with current industry experience and accepted designs and practices. Not just imagining. The baghouse (the stainless steel vessel) is simply a filter housing.
Failure to clean tubesheet, bags are sandblasted, 2. Micronics Is Your Trusted Partner for Total Engineered Filtration Solutions. Product particle size is key. May 5, 2022. On the other hand, lower than appropriately designed duct velocities will allow the collected dust to settle in the ductwork causing dust buildup and subsequent blockage. Excessive vibration in structure causing bags to rub together, 4. We offer end-to-end solutions from Filter Media to Industry-Leading Filtration Equipment, to Spare Parts & Accessories, to On-Site Field Services and In-House Laboratory Services. There may be blotches, water stains, and discoloration visible on the failed bag. If there are fats in your product, it might be that the temperatures in your baghouse are near the melting point. Come visit us at AISTech and see Gore Filtration Solutions in person. Created by the filtration experts at Parker, this 68-page guideis a valuable tool for your operations. Its the filter media (the bag in the baghouse) that will be particularly important to this discussion of baghouse problems. In pulse bags a broken cage wire can quickly tear a hole in a filter bag. ETS conducted a site visit at problem site #1 and inspected the baghouses. After assisting the client in addressing these problems, ETS conducted a program to flow balance each system.
if reduced in diameter, a sandblasting effect can occur abrading the bags. The recommendations for future installations included: Lower the vertical (can) velocity to less than 400 fpm net. Over cleaning of bags due to excessive pressure or frequency of Read the latest GE financial news releases and stories.
If your bags use clamps they must be properly tightened to insure a good seal. Some of the lessons contained in GE's new troubleshooting guide include: * How point venting for air conveyors and conveyor belts can help cement plants and others in the rock dust industry meet National Emission Standards for Hazardous Air Pollutants (NESHAP) regulations that will require plants to reduce emissions at the point they are generated. A baghouse pressure drop calculation is also an important part of your preventive maintenance approach, helping you spot the early warning signs of problems such as false air ingress. Doing. Duct work for evidence of filling due to drop out. Different dust types also require different cleaning cycles and pressures. * How proper baghouse operation in various process industries is critical during the drying process to ensure both product quality and drying production levels. Sometimes, however, it is neither a filter or a baghouse issue, but an operating problem. Provisions are usually made by the collector manufacturer to protect your bags, however, it is your responsibility to maintain these systems. Poor installation can also mean leaks inside a collector. Florida, Headquarters ETS, Inc. 1401 Municipal Road NW Roanoke, VA Tune in or catch up on GEs latest investor events and reports. Fabrication / webinfo@staclean.com / Site Map, Let 25 EXd=document;EXw?"":EXw="na";EXb?
Required fields are marked *. The GORE SO2 Control System is a catalytic, reagent-less FGD system designed to fit tight spaces, consume less water, and reduce operating costs. Beware of additives you may have in your product, for instance Lecithin that may be added in an external fluid bed to instantize and solubilize your product, as additives need to be considered in regards to correct baghouse functioning.
If caught soon enough and taken care of, a minimum of downtime may be required. There was also a complaint that several of the hoods were not operating properly, thus causing a dusty atmosphere for operations personnel.
var EXlogin='cla8857' // Login Industry experience has been relatively positive regarding premature bag wear as long as bag "bumpers" and low gas velocities are employed. Malfunction of discharge valve, screw conveyor or material transfer GE also serves the energy sector by providing technology and service solutions that are based on a commitment to quality and innovation.
Each time the filter starts up on clean bags, the smallest abrasive particles blast right through the fabric, tearing little holes as they go. Learn how were delivering on our priorities. Dampers to see that they are working. We build intelligent devices, data analytics, applications and services to enable healthcare practitioners to deliver care more efficiently and with better outcomes.
In each case the baghouse was preceded in-line by a lime spray drier for SO2 removal. var EXvsrv='s11' // VServer
A high differential pressure across the baghouse, for example, will not only reduce airflow through the system and slow production, it also can affect the retention time of the particulate in the heated gas stream. Two of the plants had previously retrofitted their baghouse hoppers to lower the can velocity and improve flow distribution in an attempt to lower the operating pressure drop and reduce the potential for bag wear. Recommended Operating Temperatures of Baghouse Felt Medias, Troubleshooting Your Baghouse Dust Collector. I do recommend changing a few bags that have prematurely failed, but changing half the collector simply puts the clean bags on double duty until they are as blinded as the old half. Is the product sensor plugged? "/"+EXvsrv+".g?login="+EXlogin+"&", Baffles to insure they are in position and have not eroded.
The company continues to invest in new technology solutions and grow through strategic acquisitions to strengthen its local presence and better serve customers around the world. "This new troubleshooting guidebook updates the old guide we created, which quickly became one of the top reference manuals for customers with dry dust collection systems," said Brian Vancrum, industrial filtration product general manager for GE Power & Water. If diaphragm valve outlet port is leaking, iii.
KANSAS CITY, MO.---November 18, 2011---To help industrial plants maximize their efficiency, improve dust collection performance, save energy and boost production, today GE (NYSE: GE) announced the introduction of its new "troubleshooting guide" that draws on the company's four decades of expertise in dust collection technology and services.
Baghouse or Dust Collector Do not take your dust collector for granted. Leaving a decent filter cake on after pulsing allows those tiny sharp particles to embed into the filter cake, preventing premature bag failure.
If the bottom six inches of the bag are the only point of abrasive failure, its likely that other cages are rubbing against it. Automatic conveyors to insure they are working. SOME COMMON SYMPTONS AND THE PROBLEMS THAT Because the issue of gas distribution design is more of an empirical art rather than a true science, we recommended a flow model analysis should be conducted to both firm up the nature of the existing gas distribution problem, and to optimize the baffle design. possible leaks in hopper. The baghouse systems at all three plants were similar in that they were of the same design, and provided by the same supplier.
Staclean Is Your Single Source Supplier for All Your Baghouse Needs. Stay up to date with the latest resources for the planned spin-offs. Answers to popular and relevant inquiries. Failure to initiate discharge device prior to start-up, 2.
"Our team has 40 years of experience solving baghouse filtration problems, and this new troubleshooting guide allows us to share that expertise to help customers quickly, conveniently and reliably address their operational priorities.". Do the roundness and size of the tubesheet holes match?