Volts per hertz driveswork well on all applications in which the load is predictable and does not change quickly. A variable-frequency drive (VFD) is a type of motor drive used in electro-mechanical drive systems to control AC motor speed and torque by varying motor input frequency and, depending on topology, to control associated voltage or current variation.
A frequency converter is an electronic device that changes the frequency and voltage of a three-phase network (output frequency and voltage control) in order to control the speed of the motor. A small amount of braking torque is available to help decelerate the load a little faster than it would stop if the motor were simply switched off and allowed to coast. A commissioning file containing records of software settings, set points and other relevant programme parameters is compiled and stored for future reference. Over time, EDM-based sparking causes erosion in the bearing race that can be seen as a fluting pattern. The drive controller can also be configured as a phase converter having single-phase converter input and three-phase inverter output.
[67], It is very common practice for power companies or their customers to impose harmonic distortion limits based on IEC or IEEE standards. Variable-frequency drives are also categorized by the following load torque and power characteristics: VFDs are available with voltage and current ratings covering a wide range of single-phase and multi-phase AC motors. 8 Electrical Braking", "Adjustable Speed Drives: Drive Up Energy Efficiency", "Guide to Variable Speed Drives Technical Guide No. This filtered DC voltage is converted to quasi-sinusoidal AC voltage output using the inverter's active switching elements. IGBT switching rates in VFDs range from 2 to 15 kHz. [9], Controller advances have exploited dramatic increases in the voltage and current ratings and switching frequency of solid-state power devices over the past six decades. Please stay us informed like this. Reduce the starting current of the motor. Jeff Conner The preferred method of speed control for squirrel-cage induction motors is to vary the frequency of the supply voltage, and the system used for this purpose is known as variable frequency drives orVFD. What Types of motors can be used with variable frequency drives? An embedded microprocessor governs the overall operation of the VFD controller. A VFD reactor, as shown in figure, is basically an inductor installed on the input or output of the drive. For example, the volt per hertz ratio for a 415 Volt, 50Hz will be 8.3 V/Hz. The introduction of control systems using a variable frequency drive is an innovative measure and usually pays for itself quickly.Variable frequency drives manufacturers offer a wide range of drives for applications involving electric motors. For example, at 63% speed a motor load consumes only 25% of its full-speed power. Many faults do not represent a failure in the VFD itself, but may mean problems with incoming power, the motor, or the driven load. [76][77][78][79], Carrier frequencies above 5kHz are likely to cause bearing damage unless protective measures are taken. Such energy cost savings are especially pronounced in variable-torque centrifugal fan and pump applications, where the load's torque and power vary with the square and cube, respectively, of the speed. Plug-in and hybrid electric vehicles of all types (see image and, This page was last edited on 20 July 2022, at 18:50. diode rectifier). Constant power, such as in machine tool and traction applications. 4", "Energy-Efficiency Policy Opportunities for Electric Motor-Driven Systems", "DC or AC Drives? In many applications, drives often have a return on investment above the price of the drive.
In some cases, the need for smooth control of the angular velocity of shafts of mechanisms is dictated by the technology itself. A variable frequency drive controls the speed, torque, and direction of an AC induction motor. A crane, where the hoist motor stops and reverses frequently, and braking is required to slow the load during lowering. The drive of this mechanism is traditionally carried out by a DC motor with adjustable speed. It is lastly useful to relate VFDs in terms of the following two classifications: CSI or VSI (six-step or PWM), cycloconverter, matrix, Capacitor assisted CSI PWM drive (legacy), Simplified Neutral Point Clamped 3-Level Inverter Topology, Simplified Cascaded H-bridge Inverter Topology, Simplified Flying Capacitor Inverter 4-Level Topology, Simplified Neutral Point Clamped H-bridge Inverter Topology. There are two types of reactive consumptions in AC power system, inductive and capacitive reactances. [81] When these high-frequency voltages find a path to earth through a bearing, transfer of metal or electrical discharge machining (EDM) sparking occurs between the bearing's ball and the bearing's race. Costs for maintenance and repairs across your lines go down, as does your electricity bill.
Certain high-performance applications involve four-quadrant loads (Quadrants I to IV) where the speed and torque can be in any direction such as in hoists, elevators, and hilly conveyors. Regenerative VFDs are widely used where speed control of overhauling loads is required. Rectified voltage, in addition to the constant component, also contains a variable, which has the form of unidirectional pulsations with a certain amplitude. The VFD controls the output current frequency by converting the input AC current to DC, then performing pulse width modulation on the voltage to obtain AC current with the required characteristics. Sorry but VFD and PIV drive are not comparable , for too many reasons , please check it out, there are articles about this issue on the web (sorry, I do not have the link). Connected downstream of inverteroutput reactor, sine wave filter, dV/dt filter. In other words, drive maintains a constant V/Hz ratio. The mains voltage is first fed to the rectifier, where it is transformed into direct current. For emerging SiC MOSFET powered drives, significant overvoltages have been observed at cable lengths as short as 3 meters. Some sources define two-quadrant drives as loads operating in quadrants I and III where the speed and torque is same (positive or negative) polarity in both directions. The VFD principle of pulse-width modulation is used to control the keys.
Control circuitry coordinates the switching of power devices to activate the power components in the right sequence. Since most large power supplies are three-phase, there will be a minimum of 6 rectifiers used. Your email address will not be published. This is sometimes called "field weakening" and, for ACmotors, means operating at less than rated V/Hz and above rated nameplate speed. Tamper-Resistant Outlet: What is it? Limit demand and electrical consumption of motors by reducing the amount of energy they consume. Two rectifiers are required for each phase of power. The variable frequency drive is correctly programmed to deliver the intended operation (and energy savings) and that this is demonstrated to operators/ engineering staff on completion. VFDs allow you to use a single motor for a variety of processes and conditions that may require different speeds. The term six-step refers strictly speaking to an inverter waveform output alternative to PWM, some drives being configured as combined six-step and PWM options. An embedded microprocessor is used for all internal logic and decision requirements. A variable-frequency drive is a device used in a drive system consisting of the following three main sub-systems: AC motor, main drive controller assembly, and drive/operator interface. In this case, during the half-period of current rise, the choke induces an EMF of the opposite direction. A load reactor helps to extend the life of the motor and increase the permittable distance between motor and drive. Motors are being used worldwide on the industrial or domestic level. No use of any material covered by this copyright may be used in whole or in part without the express written consent of Hallam-ICS. Hallam-ICS is an engineering and automation company that designs MEP systems for facilities and plants, engineers control and automation solutions, and ensures safety and regulatory compliance through arc flash studies, commissioning, and validation. For that matter, many devices are used but the best among all the devices is the Variable Frequency Drive. by throttling. Referring to the accompanying chart, drive applications can be categorized as single-quadrant, two-quadrant, or four-quadrant; the chart's four quadrants are defined as follows:[26][27][28]. The VFD may also be controlled by a programmable logic controller through Modbus or another similar interface. Certain applications involve two-quadrant loads operating in quadrant I and II where the speed is positive but the torque changes polarity as in case of a fan decelerating faster than natural mechanical losses. These machines are the cheapest, structurally simple, have no brush apparatus, and can be adapted to work in the most severe conditions. An operator interface keypad and display unit is often provided on the front of the VFD controller as shown in the photograph above. centrifugal pumps or fans) and certain constant-torque (e.g. [2][3] For example, an S-curve pattern can be applied to a conveyor application for smoother deceleration and acceleration control, which reduces the backlash that can occur when a conveyor is accelerating or decelerating. Insulation standards for three-phase motors rated 230V or less adequately protect against such long-lead overvoltages. Occasionally check to make sure all electrical connections are tight.
Most motors are designed to operate between 0 and 50 Hz, but some drives permit the output frequency to be set above 50 Hz, which would permit the motor to operate at higher than normal speed. Poor grounding of motor stators can lead to shaft-to-ground bearing currents. For example, the capacity of boilers and power units of thermal power plants is regulated by smooth change of capacity of fuel supply mechanisms. It is important to verify the maximum cable distance stated in the drive specifications, especially non-inverter-duty motors. In the half-period of current decay, the energy stored in the choke is released, preventing it from decreasing, and the capacitor is discharged to the load, also maintaining the value of current. The function of each block is as follows: Converter: It is a bridge rectifier circuit that converts the applied AC to DC. In the absence of a frequency converter, it is possible to use only one speed and rated power regardless of the load of the system at the time. Operation of the motors above rated nameplate speed (base speed) is possible, but is limited to conditions that do not require more power than the nameplate rating of the motor. Protect the motor with its internal protection functions. Variable torque, such as in centrifugal fan, pump, and blower applications, Constant torque, such as in conveyor and positive-displacement pump applications. The alternating current component, however, experiences the inductive resistance of the choke. An increasing number of end users are showing greater interest in electric drive systems due to more stringent emission standards and demand for increased reliability and better availability. VFDs produce harmonics when they convert AC to DC and DC back to AC. With over 25 years of experience in the industrial automation repair industry, Jeff Conner is the Dallas Service Manager forControl Conceptsand serves on the Advisory Committee for the Electronics Technologies Department at Texas State Technical College. This power is returned to the drive's DC link element (capacitor or reactor). The maximum hertz control can also be set to limit the output frequency to a value of less than 50 Hz, which would limit the motor speed to a value less than normal. Reducing energy cost makes perfect business sense; it saves money, enhances corporate reputation and helps everyone in the fight against climate change. Variable torque fans & pumps are good candidates for savings. Minimum Hz: This sets the minimum speed the motor is permitted to run. The presence of high-frequency components, caused by pulsations, hurts the operation of electronics, so frequency-controlled drives are usually equipped with filters of this kind. With a VFD, the stopping sequence is just the opposite as the starting sequence. The IGBT can switch on and off several thousand times per second and precisely control the power delivered to the motor. Mid-range systems are used in coal-fired power plants, mining, mills, utilities, etc. The use of mechanical gearboxes is always accompanied by considerable losses, and such systems have a limited control range. Keep the drive free of dust, ensure you have proper ventilation, and keep everything dry and protected from moisture. It is used to control the speed of an AC motor. This increased current equates to increased power consumption. * In Massachusetts, New York & North Carolina, engineering is offered/performed by Hallam Engineering, LLP. Bypass capability in the event of an emergency, Type of motor (three-phase asynchronous motor), Input voltage = rated operating voltage of the motor (for example, 3 AC~400V), Rated motor current (guide value, dependent on the circuit type and the supply voltage), Ambient temperature (rated value 122F [50C]). Thanks for reading aboutthe vfd working principle. For more details, visit Wikipedia. In such cases, the output is controlled by throttling with a damper and the head is controlled by the inlet vanes. The range of ratings is as follows: 3 kV, 3.3 kV, 4.16 kV, 6 kV, 6.6 kV, 10 kV, and 11 kV.+. On 460V or 575V systems and inverters with 3rd-generation 0.1-microsecond-rise-time IGBTs, the maximum recommended cable distance between VFD and motor is about 50m or 150feet. I am trying to develop a controller for switched reluctance motor which minimizes torque ripple.
[6] Systems using VFDs can be more efficient than those using throttling control of fluid flow, such as in systems with pumps and damper control for fans. When the switches S1 and S4 are turned ON, the current flows in the lamp in the direction of A. This is particularly evident in the case of water head or airflow in a fan. kq+/-1, where k=integer, q=pulse number of converter). Motors used with VFDs should have. Which will drive the output to a designated frequency after a power cycle, or after a fault has been cleared, or after the emergency stop signal has been restored (generally emergency stops are active low logic). How does it work? How long will a variable frequency drive last?
I am satisfied that you simply shared this helpful info with us. Permanent magnet synchronous motors have quite limited field-weakening speed range due to the constant magnet flux linkage. Thus, no braking resistor is needed, and the efficiency of the drive is improved if the drive is frequently required to brake the motor. In addition to the use of DC motors, the stepless control function is realized using mechanical variations, for example, in large machine drives. The use of a frequency drive provided with an asynchronous motors having a short-closed rotor makes it possible to eliminate the listed disadvantages of DC engines and mechanical adjustment systems. [69], A carrier frequency of at least ten times the desired output frequency is used to establish the PWM switching intervals. Advanced units use more intelligent & adaptive algorithms to improve motor performance. Which is economical considering initial,operating & maintenance costs?. [20] At higher speeds, the induction motor torque has to be limited further due to the lowering of the breakaway torque[a] of the motor. Ramping Time: VFDs have good control over acceleration and de-acceleration, which is also known as ramping. Acceleration and de-acceleration time of a VFD can be set by setting its ramping time. The harmonics treatment that follows is limited for simplication reasons to LV VSI-PWM drives. A VFD drive system could be divided into three subsystems: Over the decades, variable frequency drives have become smaller, thanks in particular to microprocessors replacing solid-state components. Remote control instructs the VFD to ignore speed commands from the keypad while local control instructs the VFD to ignore external control and only abide by the keypad.
A frequency converter is an electronic device that changes the frequency and voltage of a three-phase network (output frequency and voltage control) in order to control the speed of the motor. A small amount of braking torque is available to help decelerate the load a little faster than it would stop if the motor were simply switched off and allowed to coast. A commissioning file containing records of software settings, set points and other relevant programme parameters is compiled and stored for future reference. Over time, EDM-based sparking causes erosion in the bearing race that can be seen as a fluting pattern. The drive controller can also be configured as a phase converter having single-phase converter input and three-phase inverter output.
[67], It is very common practice for power companies or their customers to impose harmonic distortion limits based on IEC or IEEE standards. Variable-frequency drives are also categorized by the following load torque and power characteristics: VFDs are available with voltage and current ratings covering a wide range of single-phase and multi-phase AC motors. 8 Electrical Braking", "Adjustable Speed Drives: Drive Up Energy Efficiency", "Guide to Variable Speed Drives Technical Guide No. This filtered DC voltage is converted to quasi-sinusoidal AC voltage output using the inverter's active switching elements. IGBT switching rates in VFDs range from 2 to 15 kHz. [9], Controller advances have exploited dramatic increases in the voltage and current ratings and switching frequency of solid-state power devices over the past six decades. Please stay us informed like this. Reduce the starting current of the motor. Jeff Conner The preferred method of speed control for squirrel-cage induction motors is to vary the frequency of the supply voltage, and the system used for this purpose is known as variable frequency drives orVFD. What Types of motors can be used with variable frequency drives? An embedded microprocessor governs the overall operation of the VFD controller. A VFD reactor, as shown in figure, is basically an inductor installed on the input or output of the drive. For example, the volt per hertz ratio for a 415 Volt, 50Hz will be 8.3 V/Hz. The introduction of control systems using a variable frequency drive is an innovative measure and usually pays for itself quickly.Variable frequency drives manufacturers offer a wide range of drives for applications involving electric motors. For example, at 63% speed a motor load consumes only 25% of its full-speed power. Many faults do not represent a failure in the VFD itself, but may mean problems with incoming power, the motor, or the driven load. [76][77][78][79], Carrier frequencies above 5kHz are likely to cause bearing damage unless protective measures are taken. Such energy cost savings are especially pronounced in variable-torque centrifugal fan and pump applications, where the load's torque and power vary with the square and cube, respectively, of the speed. Plug-in and hybrid electric vehicles of all types (see image and, This page was last edited on 20 July 2022, at 18:50. diode rectifier). Constant power, such as in machine tool and traction applications. 4", "Energy-Efficiency Policy Opportunities for Electric Motor-Driven Systems", "DC or AC Drives? In many applications, drives often have a return on investment above the price of the drive.

Certain high-performance applications involve four-quadrant loads (Quadrants I to IV) where the speed and torque can be in any direction such as in hoists, elevators, and hilly conveyors. Regenerative VFDs are widely used where speed control of overhauling loads is required. Rectified voltage, in addition to the constant component, also contains a variable, which has the form of unidirectional pulsations with a certain amplitude. The VFD controls the output current frequency by converting the input AC current to DC, then performing pulse width modulation on the voltage to obtain AC current with the required characteristics. Sorry but VFD and PIV drive are not comparable , for too many reasons , please check it out, there are articles about this issue on the web (sorry, I do not have the link). Connected downstream of inverteroutput reactor, sine wave filter, dV/dt filter. In other words, drive maintains a constant V/Hz ratio. The mains voltage is first fed to the rectifier, where it is transformed into direct current. For emerging SiC MOSFET powered drives, significant overvoltages have been observed at cable lengths as short as 3 meters. Some sources define two-quadrant drives as loads operating in quadrants I and III where the speed and torque is same (positive or negative) polarity in both directions. The VFD principle of pulse-width modulation is used to control the keys.
Control circuitry coordinates the switching of power devices to activate the power components in the right sequence. Since most large power supplies are three-phase, there will be a minimum of 6 rectifiers used. Your email address will not be published. This is sometimes called "field weakening" and, for ACmotors, means operating at less than rated V/Hz and above rated nameplate speed. Tamper-Resistant Outlet: What is it? Limit demand and electrical consumption of motors by reducing the amount of energy they consume. Two rectifiers are required for each phase of power. The variable frequency drive is correctly programmed to deliver the intended operation (and energy savings) and that this is demonstrated to operators/ engineering staff on completion. VFDs allow you to use a single motor for a variety of processes and conditions that may require different speeds. The term six-step refers strictly speaking to an inverter waveform output alternative to PWM, some drives being configured as combined six-step and PWM options. An embedded microprocessor is used for all internal logic and decision requirements. A variable-frequency drive is a device used in a drive system consisting of the following three main sub-systems: AC motor, main drive controller assembly, and drive/operator interface. In this case, during the half-period of current rise, the choke induces an EMF of the opposite direction. A load reactor helps to extend the life of the motor and increase the permittable distance between motor and drive. Motors are being used worldwide on the industrial or domestic level. No use of any material covered by this copyright may be used in whole or in part without the express written consent of Hallam-ICS. Hallam-ICS is an engineering and automation company that designs MEP systems for facilities and plants, engineers control and automation solutions, and ensures safety and regulatory compliance through arc flash studies, commissioning, and validation. For that matter, many devices are used but the best among all the devices is the Variable Frequency Drive. by throttling. Referring to the accompanying chart, drive applications can be categorized as single-quadrant, two-quadrant, or four-quadrant; the chart's four quadrants are defined as follows:[26][27][28]. The VFD may also be controlled by a programmable logic controller through Modbus or another similar interface. Certain applications involve two-quadrant loads operating in quadrant I and II where the speed is positive but the torque changes polarity as in case of a fan decelerating faster than natural mechanical losses. These machines are the cheapest, structurally simple, have no brush apparatus, and can be adapted to work in the most severe conditions. An operator interface keypad and display unit is often provided on the front of the VFD controller as shown in the photograph above. centrifugal pumps or fans) and certain constant-torque (e.g. [2][3] For example, an S-curve pattern can be applied to a conveyor application for smoother deceleration and acceleration control, which reduces the backlash that can occur when a conveyor is accelerating or decelerating. Insulation standards for three-phase motors rated 230V or less adequately protect against such long-lead overvoltages. Occasionally check to make sure all electrical connections are tight.
Most motors are designed to operate between 0 and 50 Hz, but some drives permit the output frequency to be set above 50 Hz, which would permit the motor to operate at higher than normal speed. Poor grounding of motor stators can lead to shaft-to-ground bearing currents. For example, the capacity of boilers and power units of thermal power plants is regulated by smooth change of capacity of fuel supply mechanisms. It is important to verify the maximum cable distance stated in the drive specifications, especially non-inverter-duty motors. In the half-period of current decay, the energy stored in the choke is released, preventing it from decreasing, and the capacitor is discharged to the load, also maintaining the value of current. The function of each block is as follows: Converter: It is a bridge rectifier circuit that converts the applied AC to DC. In the absence of a frequency converter, it is possible to use only one speed and rated power regardless of the load of the system at the time. Operation of the motors above rated nameplate speed (base speed) is possible, but is limited to conditions that do not require more power than the nameplate rating of the motor. Protect the motor with its internal protection functions. Variable torque, such as in centrifugal fan, pump, and blower applications, Constant torque, such as in conveyor and positive-displacement pump applications. The alternating current component, however, experiences the inductive resistance of the choke. An increasing number of end users are showing greater interest in electric drive systems due to more stringent emission standards and demand for increased reliability and better availability. VFDs produce harmonics when they convert AC to DC and DC back to AC. With over 25 years of experience in the industrial automation repair industry, Jeff Conner is the Dallas Service Manager forControl Conceptsand serves on the Advisory Committee for the Electronics Technologies Department at Texas State Technical College. This power is returned to the drive's DC link element (capacitor or reactor). The maximum hertz control can also be set to limit the output frequency to a value of less than 50 Hz, which would limit the motor speed to a value less than normal. Reducing energy cost makes perfect business sense; it saves money, enhances corporate reputation and helps everyone in the fight against climate change. Variable torque fans & pumps are good candidates for savings. Minimum Hz: This sets the minimum speed the motor is permitted to run. The presence of high-frequency components, caused by pulsations, hurts the operation of electronics, so frequency-controlled drives are usually equipped with filters of this kind. With a VFD, the stopping sequence is just the opposite as the starting sequence. The IGBT can switch on and off several thousand times per second and precisely control the power delivered to the motor. Mid-range systems are used in coal-fired power plants, mining, mills, utilities, etc. The use of mechanical gearboxes is always accompanied by considerable losses, and such systems have a limited control range. Keep the drive free of dust, ensure you have proper ventilation, and keep everything dry and protected from moisture. It is used to control the speed of an AC motor. This increased current equates to increased power consumption. * In Massachusetts, New York & North Carolina, engineering is offered/performed by Hallam Engineering, LLP. Bypass capability in the event of an emergency, Type of motor (three-phase asynchronous motor), Input voltage = rated operating voltage of the motor (for example, 3 AC~400V), Rated motor current (guide value, dependent on the circuit type and the supply voltage), Ambient temperature (rated value 122F [50C]). Thanks for reading aboutthe vfd working principle. For more details, visit Wikipedia. In such cases, the output is controlled by throttling with a damper and the head is controlled by the inlet vanes. The range of ratings is as follows: 3 kV, 3.3 kV, 4.16 kV, 6 kV, 6.6 kV, 10 kV, and 11 kV.+. On 460V or 575V systems and inverters with 3rd-generation 0.1-microsecond-rise-time IGBTs, the maximum recommended cable distance between VFD and motor is about 50m or 150feet. I am trying to develop a controller for switched reluctance motor which minimizes torque ripple.
[6] Systems using VFDs can be more efficient than those using throttling control of fluid flow, such as in systems with pumps and damper control for fans. When the switches S1 and S4 are turned ON, the current flows in the lamp in the direction of A. This is particularly evident in the case of water head or airflow in a fan. kq+/-1, where k=integer, q=pulse number of converter). Motors used with VFDs should have. Which will drive the output to a designated frequency after a power cycle, or after a fault has been cleared, or after the emergency stop signal has been restored (generally emergency stops are active low logic). How does it work? How long will a variable frequency drive last?
I am satisfied that you simply shared this helpful info with us. Permanent magnet synchronous motors have quite limited field-weakening speed range due to the constant magnet flux linkage. Thus, no braking resistor is needed, and the efficiency of the drive is improved if the drive is frequently required to brake the motor. In addition to the use of DC motors, the stepless control function is realized using mechanical variations, for example, in large machine drives. The use of a frequency drive provided with an asynchronous motors having a short-closed rotor makes it possible to eliminate the listed disadvantages of DC engines and mechanical adjustment systems. [69], A carrier frequency of at least ten times the desired output frequency is used to establish the PWM switching intervals. Advanced units use more intelligent & adaptive algorithms to improve motor performance. Which is economical considering initial,operating & maintenance costs?. [20] At higher speeds, the induction motor torque has to be limited further due to the lowering of the breakaway torque[a] of the motor. Ramping Time: VFDs have good control over acceleration and de-acceleration, which is also known as ramping. Acceleration and de-acceleration time of a VFD can be set by setting its ramping time. The harmonics treatment that follows is limited for simplication reasons to LV VSI-PWM drives. A VFD drive system could be divided into three subsystems: Over the decades, variable frequency drives have become smaller, thanks in particular to microprocessors replacing solid-state components. Remote control instructs the VFD to ignore speed commands from the keypad while local control instructs the VFD to ignore external control and only abide by the keypad.
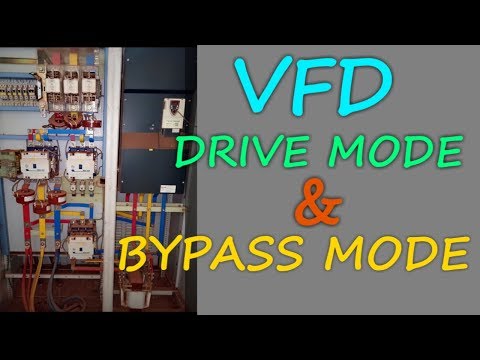