Plastics are made of petrochemical hydrocarbons with additives such as flame-retardants, stabilizer, and oxidants that make it difficult to bio-degrade (Ma et al., 2017). TG/FTIR analysis on co-pyrolysis behavior of PE, PVC and PS. Biorefineries have a great potential to convert waste into energy and other valuable products and could help to achieve circular economies. liquefaction pyrolysis In addition, the presence of the oxygen atom also favors the high production of char from catalytic pyrolysis of PET (Xue et al., 2017). (2004). Although pyrolysis oil holds more energy than coal and some other fuels, pyrolysis itself is an energy-intensive process, and the oil product requires more energy to be refined (Inman, 2012). Vol. Polym. The functional groups in pyrolysis oil was analyzed by a FT-IR, Perkin Elmer's, UK instrument. are basically shown in Figure 5.3, Waste plastics as a reactant for obtaining the valuable products are invariably contaminated with materials such as soil, iron and wood etc. Batool et al. Catalytic pyrolysis of plastic waste: a review. The availability of plastic and biomass waste streams as feedstocks for pyrolysis based biorefineries, is another major challenge, since recycling is not currently very efficient, especially in the developing countries. Proc. 34, 676682. The LCA can analyze the environmental impact of the biorefinery and all products by conducting detailed energy and material balances of all life stages including raw material extraction and processing, manufacturing, product distribution, use, maintenance, and disposal/recycling. 58, 250259. The high yield of liquid oil from catalytic pyrolysis of PS was also reported in several other studies (Siddiqui and Redhwi, 2009; Lee, 2012; Rehan et al., 2017). The liquid oil produced from catalytic pyrolysis of PS, with both activated catalysts, mainly contains aromatic hydrocarbons with some paraffins, naphthalene and olefin compounds (Rehan et al., 2017). (2017). NZ was crushed into powder (<100 nm) in a ball-milling machine (Retsch MM 480) for 3 h using 20 Hz/sec, before modification and its usage in pyrolysis. (2012) and Panda and Singh (2013) also reported the presence of aromatics with some alkanes and alkenes from catalytic pyrolysis of PP. The initial degradation of PET was perhaps due to the presence of some volatile impurities such as diethylene glycol (Dimitrov et al., 2013). doi: 10.1002/1097-4628(20000829)77:9<1894::AID-APP5>3.0.CO;2-Y, Frigo, S., Seggiani, M., Puccini, M., and Vitolo, S. (2014). Front. Pyrolysis of a fraction of waste polypropylene and polyethylene for the recovery of BTX aromatics using a fluidized bed reactor. The small pilot scale reactor has the capability to be used as both a thermal and catalytic pyrolysis, using different feedstocks such as plastic and biomass materials (Figure 1). doi: 10.1016/j.apenergy.2016.04.116, Obali, Z., Sezgi, N. A., and Dou, T. (2012). The characteristics of this process are the quality of the oil product, very similar to that of conventional gasoline, kerosene and diesel oils, but the drawback of the catalyst is high cost and short life-cycle due to poisoning/deactivation. Eng. Further, the hydrogenation steps occurred, leading to the synthesis of secondary free-radicals (new stable C-H bond), which resulted into -scission and produced an unsaturated group (Rizzarelli et al., 2016). The higher production was perhaps due to the presence of high acidic sites, as it favors phenol compound production. The catalytic pyrolysis of different types of plastics waste (PS, PE, PP, and PET) as single or mixed in different ratios, in the presence of modified natural zeolite (NZ) catalysts in a small pilot scale pyrolysis reactor, was carried out for the first time. Volatile products of poly (ethylene terephthalate) thermal degradation in nitrogen atmosphere. Sci. Catalytic degradation of polystyrene over natural clinoptilolite zeolite. 76, 4552. (2004) reported highly reactive olefin production, as intermediate products during the catalytic pyrolysis of PE, that may favor the production of paraffin and aromatic compounds in produced liquid oil. Recyling of plastic wastes via pyrolysis. The produced liquid oil characterization was carried out to investigate the effect of feedstock composition on the quality of liquid oil produced in the presence of modified NZ. Several researchers activated the char via steam and thermal activation (Lopez et al., 2009; Heras et al., 2014). Sci. (2014) reported that AA-NZ with HCl has high acidity compared to TA-NZ, produced less liquid oil yield and had high production of gases. The produced liquid oil from catalytic pyrolysis of PE/PP contains aromatic, olefin, and naphthalene compounds. Moreover, the presence of a high acidic site on catalysts enhanced the oligomerization, aromatization and deoxygenation mechanism that led to the production of poly-aromatic and naphthalene compounds. On the contrary, this process has problems with toleration in the chlorine produced, the removal of solid sludge from the fluidized bed and also its long-term durability. Figure 2. Pyrolysis 117,7281. (2004). Waste Manag. Sci. doi: 10.1016/S0921-3449(00)00052-5, Kunwar, B., Moser, B. R., Chandrasekaran, S. R., Rajagopalan, N., and Sharma, B. K. (2016). 51, 96102. However, when PP and PE catalytic pyrolysis was carried out separately with PS, a significant difference was observed in the product yield. Polym. IOSR J. Mech. The potential of Saudi Arabian natural zeolites in energy recovery technologies. Effect of blend ratio of plastic pyrolysis oil and diesel fuel on the performance of single cylinder CI engine. Stab. doi: 10.1016/B978-0-444-64017-8.00017-8. PP degradation started at a very low temperature (240C) compared to other feedstocks. The catalytic pyrolysis of individual PS plastic using TA-NZ and AA-NZ catalysts showed the highest liquid oil yields of 70 and 60%, respectively, compared to all other types of individual and combined plastic waste studied. The chemical composition of liquid oil produced by the catalytic pyrolysis of different plastic waste using TA-NZ and AA-NZ catalysts were characterized by GC-MS (Figures 4, 5). Catalytic conversion of polyolefins into liquid fuels over MCM-41: comparison with ZSM-5 and amorphous SiO2Al2O3. The liquid oil produced from the catalytic pyrolysis of PE, when using both catalysts, produced mainly Naphthalene, Phenanthrene, Naphthalene, 2-ethenyl-, 1-Pentadecene, Anthracene, 2-methyl-, Hexadecane and so on (Figures 4A, 5A). Yield and composition of gases and oils/waxes from the feedstock recycling of waste plastic. In Feeds Tock Recycling and Pyrolysis of Waste Plastics: Converting Waste Plastics into Diesel and Other Fuels, eds J. Scheirs and W. Kaminsky (West Sussex: John Wiley & Sons Press), 285309. The use of synthetic catalysts enhanced the overall pyrolysis process and improved the quality of produced liquid oil. (2014) carried out TGA of PS with PE and reported that the presence of PS favors the degradation of PE, due to the production of stable benzene rings. (1982) carried out pyrolysis of PS with the alumina-silica catalyst at 300C and found the hydrogenation of styrene to its derivate. Stab. The obtained data revealed the presence of aromatics and aliphatic functional groups in the oil (Figures 6, 7). Eng. (2014) also reported that catalytic pyrolysis of PP and PS with an acid (HCL) activated natural zeolite catalyst produced more gases than the process with a thermally activated natural zeolite catalyst, due to its high acidity and BET surface area. Moreover, formation of carbocation during PP degradation, due to the presence of tertiary carbon in its carbon chain, may also favor gas production (Jung et al., 2010). Activation of waste tire char by cyclic liquid-phase oxidation. If it contains a lot of various contaminative materials in waste plastics, it leads to poor economics by increasing the recycling procedure cost. Gaca et al. Furthermore, liquid oil produced from different types of plastic waste had higher heating values (HHV) in the range of 41.744.2 MJ/kg similar to that of conventional diesel. Bernando, M. (2011). The residence time of plastics in the reactor depends on the plastic type and the desired viscosity extent. TGA was carried out on feedstock to obtain the optimal process conditions such as temperature and reaction time (75 min) under controlled conditions. 74, 297305. All types of plastic waste show similar degradation behavior with the rapid loss of weight of hydrocarbons within the narrow range of temperature (150250C) (Figure 2). Untapped conversion of plastic waste char into carbon-metal LDOs for the adsorption of Congo red. Figure 7. doi: 10.1016/j.jaap.2011.12.015, Lee, S., Yoshida, K., and Yoshikawa, K. (2015).
doi: 10.1016/j.wasman.2011.05.021, Lopez, G., Olazar, M., Artetxe, M., Amutio, M., Elordi, G., and Bilbao, J. Biodegrad. In TGA, a 10 g of each type of plastic waste was taken and heated with a rate of 10C from 25 to 900C under a continuous flow of nitrogen (50 ml/min). By preheating the plastic feedstock the melting time in the melting reactor can be shorted thus improving production rates. Pyrolysisgasification of plastics, mixed plastics and real-world plastic waste with and without NiMgAl catalyst. Pyrol. Figure 3. The high aromatic contents of the pyrolysis oil is good and some aromatic compounds such as benzene, toluene, and styrene can be refined and sold in an already established market. The fluidized-bed process yields a uniform product and a high conversion during a short reaction time. doi: 10.1021/ie980341+, Ukei, H., Hirose, T., Horikawa, S., Takai, Y., Taka, M., Azuma, N., et al. 14 Articles, This article is part of the Research Topic, Creative Commons Attribution License (CC BY). Furthermore the cost of transportation, labor and maintenance may increase the cost of recycling projects (Gandidi et al., 2018). Some advantages are high-quality product, low energy requirement supplied by combustion of a portion of the gas by-product, good temperature control, the efficient removal of impurities present in the waste plastic, application on a relatively small scale, and also a robust and relatively inexpensive process to establish. A., and Dwyer, J. Stab. The plastic waste used as the feedstock in the catalytic pyrolysis process was collected from Jeddah and included grocery bags, disposable juice cups and plates, and drinking water bottles, which consist of polyethylene (PE), polypropylene (PP) polystyrene (PS), and polyethylene terephthalate (PET) plastics, respectively. Catalytic conversion of polystyrene over HMCM-41, HZSM-5 and amorphous SiO2Al2O3: comparison with thermal cracking. For the processes of different reactor types, kiln and retort pyrolysis processes are characterized by a relatively low capital investment. Stab. Lee (2012) reported that PS degradation occurred via both random-chain and end chain scissions, thus leading to the production of the stable benzene ring structure, which enhances further cracking and may increase liquid oil production.
doi: 10.1016/j.wasman.2011.05.021, Lopez, G., Olazar, M., Artetxe, M., Amutio, M., Elordi, G., and Bilbao, J. Biodegrad. In TGA, a 10 g of each type of plastic waste was taken and heated with a rate of 10C from 25 to 900C under a continuous flow of nitrogen (50 ml/min). By preheating the plastic feedstock the melting time in the melting reactor can be shorted thus improving production rates. Pyrolysisgasification of plastics, mixed plastics and real-world plastic waste with and without NiMgAl catalyst. Pyrol. Figure 3. The high aromatic contents of the pyrolysis oil is good and some aromatic compounds such as benzene, toluene, and styrene can be refined and sold in an already established market. The fluidized-bed process yields a uniform product and a high conversion during a short reaction time. doi: 10.1021/ie980341+, Ukei, H., Hirose, T., Horikawa, S., Takai, Y., Taka, M., Azuma, N., et al. 14 Articles, This article is part of the Research Topic, Creative Commons Attribution License (CC BY). Furthermore the cost of transportation, labor and maintenance may increase the cost of recycling projects (Gandidi et al., 2018). Some advantages are high-quality product, low energy requirement supplied by combustion of a portion of the gas by-product, good temperature control, the efficient removal of impurities present in the waste plastic, application on a relatively small scale, and also a robust and relatively inexpensive process to establish. A., and Dwyer, J. Stab. The plastic waste used as the feedstock in the catalytic pyrolysis process was collected from Jeddah and included grocery bags, disposable juice cups and plates, and drinking water bottles, which consist of polyethylene (PE), polypropylene (PP) polystyrene (PS), and polyethylene terephthalate (PET) plastics, respectively. Catalytic conversion of polystyrene over HMCM-41, HZSM-5 and amorphous SiO2Al2O3: comparison with thermal cracking. For the processes of different reactor types, kiln and retort pyrolysis processes are characterized by a relatively low capital investment. Stab. Lee (2012) reported that PS degradation occurred via both random-chain and end chain scissions, thus leading to the production of the stable benzene ring structure, which enhances further cracking and may increase liquid oil production.
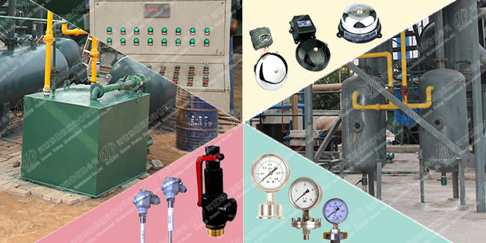


