Most dont even have a classic holding screw. What is the relationship between algorithms and logic? This is how fast you're cutting the work. A pivot point disengages the worm gear, while bearings provide it controlled movement from the worm wheel. What if you could convert your drill press into a mill instead? With double angular bearing its should improve. We are a national retailer of individual components and not all products depicted on this website are legal in every state.
| Sitemap. The head is little more than a plastic cover for protecting the belt and machinery inside. This is a HUGE Difference. The primary difference between the Broken Arms and Elite Builder are the cutting templates: The Elite Builder uses more conventional cutting guides and fewer pilot hole templates.
That will be good for positioning.
It's dangerous, but possible. For instance most routers run 20k+ RPM, while a drill press might run between 600-3000 rpm. On several of the mini-mils I have seen guys then put Teflon or brass gibs down to erode/wear versus having another anodized surface to rub or run on.
How do I know if my power drill needs to rotate clockwise or counter clockwise to drill forward? The best answers are voted up and rise to the top, Start here for a quick overview of the site, Detailed answers to any questions you might have, Discuss the workings and policies of this site, Learn more about Stack Overflow the company.
Milling Machine Attachment for Drill Press 1969 How-To build PLANS, {"modules":["unloadOptimization","bandwidthDetection"],"unloadOptimization":{"browsers":{"Firefox":true,"Chrome":true}},"bandwidthDetection":{"url":"https://ir.ebaystatic.com/cr/v/c1/thirtysevens.jpg","maxViews":4,"imgSize":37,"expiry":300000,"timeout":250}}. Suggesting that its possible to do so is just irresponsible.
The drill press's motor is an electric high-torque motor that drives the machine using belts inside the head. Obviously he cannot take heavy cuts, and hell struggle with surface finish with a 0.005 runout potentially oscillating between rigidity issues and rubbing during a single rotation of the spindle, especially for deeper depths of cut and harder materials. hundred RPM, you must go slowly. Copyright This effectively makes the arbor and chuck one unit, which will dramatically reduce runout and vibration.
Maximum amount of digits: 6. Interesting that you mention the fine valve lapping compound. Stack Exchange network consists of 181 Q&A communities including Stack Overflow, the largest, most trusted online community for developers to learn, share their knowledge, and build their careers. At best, this will invite the bit to chatter. That's okay, because a decent upgrade will run you less than $50. Wear on the spindle slide won't be an issue in my lifetime. And you know how side-lash is on a mill, the lash comes out and you hit a hard point.
How can I make points equally spaced along any line? It works largely like the Broken Arms Jig and allows the builder to complete the 80% lower largely with vertical loads. You'll use the handle every time you drill to control the depth of the bit. Other options are online machine shops or hiring a local machine shop. padawan liked Minamil: a minimal CNC mill. The item you've selected was not added to your cart. Backlash in a crappy x-y vise can cause the tool to be pulled into the workpiece, especially with conventional vs. climb milling. This replaces the press-fit JT33 connection between the chuck and arbor with a threaded connection. You're better of buying a real mill, and by that I don't mean a cheap hobby mill which looks like just a drill press with an X-Y table: a square column (or dovetail slides) and a proper locking arbor are essential. Creating excess load on the arbor, causing it to fall out. Most mill conversions are good at first but will generate wobble and runout after use in position for extended periods. Lawyer says bumping softwares minor version would cost $2k to refile copyright paperwork. Real time inventory. It uses center-cut end mills, allowing you to make plunge cuts when cleaning up the receiver's floor. If you bought a basic drill press from the local hardware store, the chuck it came with is probably inadequate for this operation. Also dont worry he used SUPER GLUE!!! Love the swapping and changing form metric to imperial lol..
You may not see any particular variance- but like anything it is a known issue among drill presses. A keyless knurled chuck provides a better bit clamp and makes for easy tooling changes without the need for a key. You dont want steel against steel or youll really mess up the quill. That means when that vibration produced by an interrupted cut during a milling operation can and WILL cause the shank to loosen from the quill and out comes the drill chuck or whatever is shoved up into the drill press. Techshop is the most well-known, but there are many others. On a typical mill (which can spin at thousands of RPM) billet or forged aluminum can be milled quickly, around 280 to 300 feet per minute. The Anodizing creates an aluminum oxide layer (very tough) that is the actual bearing surface. I thought of doing the same thing, adding an xy table to my drill press.
Most of the import machines have a fair amount of run out. Watch for wear in the aluminum ways,keep them clean and adjusted. Columbia, PA 17512 This key locks and unlocks the chuck, allowing bits to be seated or removed. By clicking Post Your Answer, you agree to our terms of service, privacy policy and cookie policy.
The This is one of the most important tips you can use to ensure you're milling with your drill as safely as possible. The jig's plates guide the bit along the receiver's walls to make the final polishing cuts. Shipping of various products found on this website are prohibited to some states (such as California, Connecticut, District of Columbia, Hawaii, New Jersey, New York, Rhode Island, and Washington). He took some steps to improve the quill, spindle, and bearings boring down the quill, replacing the bearings, and finally turning and re-threading the spindle it at 1/2-20. This sounds counter to everything we're saying but you'll come to find that using drill bits to remove most of the aluminum from your 80% lower is actually just as easy, and probably faster, than milling altogether. You can use fancy angular contact bearings, but a stack of lots of deep groove ball bearings is a pretty good approximation at a vastly lower price.
Is it possible to use a drill press as a milling machine with the proper bit? "Negating" a sentence (by adding, perhaps, "no" or "don't") gives the same meaning, Is it possible to turn rockets without fuel just like in KSP, Is there a better way of defining a constraint on positive integer variables such that no two variables are the same and are uniquely assigned a value. If you want to complete most of your receiver with drill bits and avoid any and all milling save for light polishing, this is the jig for you. The shaft of the handle is about 1 and the gear hole is 3/16. var today = new Date() The really critical thing is the spindle bearings and if he upgraded those to take side load some you should be able to use it. Someone who is told something can't be done but figures out a way to do it might not realize the dangers lurking therein.
These two factors play a bigger role than normal when machining a lower receiver, so be sure to secure the drill with the base before working.
The bit is pushed up into the machine, preserving tapered connections. If it ever does, the spindle bearings are easy enough to tighten back up. I don't know exactly what to call them. Aluminum, depending on the alloy, tends to be a little grabbier than brass. The biggest difference is speed.
That and repeated use with any lateral pressure is likely to pop the chuck right off arbor of that cheapo press. You can compensate by feeding slower, but typically small mills don't turn that much faster than drill presses using similar diameter tools in similar materials (as you might expect). As it spins up, it rotates the arbor and chuck to do work. To subscribe to this RSS feed, copy and paste this URL into your RSS reader. Then I opened the chuck up all the way and fed a 10-32 button head through the existing hole inside the chuck and screwed it tightly on to the spindle.
You should maintain a low feedrate (SFM) of 1 foot per minute when milling with your drill. At 80-lower.com, we are by no means providing this content on our website to serve as legal advice or legal counsel. Simple drill presses operate at one speed and have only an ON/OFF switch. The base holds the drill press to your workbench or floor. If you're using only a drill press, you want a jig that removes most of the aluminum from your 80% lower using drill bits and vertical machining. Uhh, this is asking for a nasty injury those chucks and drill presses are not designed for side loads. Folks have been known to glue the taper in place.
This is called bootstrapping, weve all had to do it at some point. Imperial units are fine for height/weight/distance where precision isnt important, but the system is dead. var year = today.getFullYear() Beats the $500+ mill from Horrible Freight mill being dumped upside down in the driveway by FedEx, No kidding, my mini lathe shifted on the ups truck, both the mounting bolts were totally wrecked and the chip tray was destroyed.
Before we dive into machining a firearm, you should familiarize yourself with the drill press's components. . I think they are just saying its kind of dumb to do so for most people because most people are just going to get the x-y table and MAYBE some real end mills, not even bother with better bearings and go to town, destroying their perfectly good drill press in the process.
Most of your work can (and should) be completed with vertical drilling and cutting. It only takes a minute to sign up.
:-) BTW If you havent already done this, you might like to put a little slug of brass rod in your quill lock hole before screwing the lock lever in. Ive never worked in any technical field in the US that didnt use metric when given the option. Took 2 motor replacement before we found out why it was happening. The only kind of milling on a drill press I would consider would be making a shallow groove in a soft material like wood or plastic, using a very slow feed. Much better than using a hack saw and file to make the cut, like many probably do. You have the choice of only drilling the first set of pilot holes before using conventional milling. All that said, about 99% of the Chinese hobby mill drills and combo lathe + mills just have a standard chuck with no draw-bar so doing your own conversion shouldn't be any more 'dangerous' than using a commercial (if badly designed) machine.
I give it a solid kudos. They're called hackerspaces, and if you're in or near a big city there should be one. With the adjustments, he was able to add in a cheap drill chuck, which fit in quite nicely with just a slight wobble of 5 thousandths on either side.
A drill press isn't designed to mill, but lightly milling an 80% lower can be done safely. A deeper cut invites more runout and chatter, increasing the risk of slipped tooling. Even better, you can also upgrade your Morse-tapered arbor to eliminate one potential point of failure entirely. The best way to mill with a drill press is too, well, simply avoid it as much as possible. Which is why he threaded the spindle 1/2-20. How did you mount the Boston G-1027 gear on the drill press handle? Generally, you should maintain a shallow cutting depth (0.2" or less) when milling with your drill. Also, the lack of a power feed will exacerbate surface finish problems. No backorders. It uses open template guides, allowing your end mill bits to ride along the edge of the jig for stability. Its an area that has a lot of questions that, without the correct answers, could have some serious implications. From the crappy bearings to the crappy motor to the lack of rigidity. Assuming you get the bit speed right, the downside to your plan is premature wear of the bearings on the drill press. The column is made of a solid outer tube with a solid inner tube that can be raised and lowered via the handle.
(Comment Policy). No Ferrari engine in a Lada, and no loud proclamations of racecar-like performance. Redoing those with decent bearings is necessary and why this project is a good idea rather than a failure in motion. That argument reminds me of the guys who tried to use a running lawnmower to trim their hedges. This is hackaday at its finest taking something that is useful and hacking it to make it more useful using little more than ingenuity, time and components appropriate to the original item. While its not perfect, its still significantly less expensive than buying a mill! Picked up an 80% lower for an AR-15 build?
A man with two clocks is never sure.
The handle has measurements to indicate your bit's depth.
David, if that ever happens to you again just put a light film of fine valve lapping compound on the chuck adapter then set the chuck on there and give it a few twists by hand then clean out the chuck socket and adapter.
Invariably the vibrations from the mill cutter and the fact that the cutter itself is trying to pull 'down' due to the flutes in the cutter, it will dislodge the entire chuck from the machine. Does the title of a master program makes a difference for a later PhD? This. Hey Nice job! This pulls the bit away from the machine, potentially separating the tapered connections between the chuck, arbor, and spindle. Cosmin Dumitru has updated details to CanSat Romania - Monitoring air pollution. Im a professional machinist and Im not going to boo the guy. Ah, thanks for the respose. Only digits are allowed. How can I get an AnyDice conditional to convert a sequence to a boolean?
There have been many articles in modelling magazines like Model Engineer about fixing this both on cheap mills and converted drill presses. I think you'd be hard pressed to have enough speed to handle such an operation. This is required to ensure minimal vibration and runout while you work. Doing it safely won't take long.
| Sitemap. The head is little more than a plastic cover for protecting the belt and machinery inside. This is a HUGE Difference. The primary difference between the Broken Arms and Elite Builder are the cutting templates: The Elite Builder uses more conventional cutting guides and fewer pilot hole templates.
That will be good for positioning.
It's dangerous, but possible. For instance most routers run 20k+ RPM, while a drill press might run between 600-3000 rpm. On several of the mini-mils I have seen guys then put Teflon or brass gibs down to erode/wear versus having another anodized surface to rub or run on.
How do I know if my power drill needs to rotate clockwise or counter clockwise to drill forward? The best answers are voted up and rise to the top, Start here for a quick overview of the site, Detailed answers to any questions you might have, Discuss the workings and policies of this site, Learn more about Stack Overflow the company.
Milling Machine Attachment for Drill Press 1969 How-To build PLANS, {"modules":["unloadOptimization","bandwidthDetection"],"unloadOptimization":{"browsers":{"Firefox":true,"Chrome":true}},"bandwidthDetection":{"url":"https://ir.ebaystatic.com/cr/v/c1/thirtysevens.jpg","maxViews":4,"imgSize":37,"expiry":300000,"timeout":250}}. Suggesting that its possible to do so is just irresponsible.
The drill press's motor is an electric high-torque motor that drives the machine using belts inside the head. Obviously he cannot take heavy cuts, and hell struggle with surface finish with a 0.005 runout potentially oscillating between rigidity issues and rubbing during a single rotation of the spindle, especially for deeper depths of cut and harder materials. hundred RPM, you must go slowly. Copyright This effectively makes the arbor and chuck one unit, which will dramatically reduce runout and vibration.
Maximum amount of digits: 6. Interesting that you mention the fine valve lapping compound. Stack Exchange network consists of 181 Q&A communities including Stack Overflow, the largest, most trusted online community for developers to learn, share their knowledge, and build their careers. At best, this will invite the bit to chatter. That's okay, because a decent upgrade will run you less than $50. Wear on the spindle slide won't be an issue in my lifetime. And you know how side-lash is on a mill, the lash comes out and you hit a hard point.
How can I make points equally spaced along any line? It works largely like the Broken Arms Jig and allows the builder to complete the 80% lower largely with vertical loads. You'll use the handle every time you drill to control the depth of the bit. Other options are online machine shops or hiring a local machine shop. padawan liked Minamil: a minimal CNC mill. The item you've selected was not added to your cart. Backlash in a crappy x-y vise can cause the tool to be pulled into the workpiece, especially with conventional vs. climb milling. This replaces the press-fit JT33 connection between the chuck and arbor with a threaded connection. You're better of buying a real mill, and by that I don't mean a cheap hobby mill which looks like just a drill press with an X-Y table: a square column (or dovetail slides) and a proper locking arbor are essential. Creating excess load on the arbor, causing it to fall out. Most mill conversions are good at first but will generate wobble and runout after use in position for extended periods. Lawyer says bumping softwares minor version would cost $2k to refile copyright paperwork. Real time inventory. It uses center-cut end mills, allowing you to make plunge cuts when cleaning up the receiver's floor. If you bought a basic drill press from the local hardware store, the chuck it came with is probably inadequate for this operation. Also dont worry he used SUPER GLUE!!! Love the swapping and changing form metric to imperial lol..
You may not see any particular variance- but like anything it is a known issue among drill presses. A keyless knurled chuck provides a better bit clamp and makes for easy tooling changes without the need for a key. You dont want steel against steel or youll really mess up the quill. That means when that vibration produced by an interrupted cut during a milling operation can and WILL cause the shank to loosen from the quill and out comes the drill chuck or whatever is shoved up into the drill press. Techshop is the most well-known, but there are many others. On a typical mill (which can spin at thousands of RPM) billet or forged aluminum can be milled quickly, around 280 to 300 feet per minute. The Anodizing creates an aluminum oxide layer (very tough) that is the actual bearing surface. I thought of doing the same thing, adding an xy table to my drill press.
Most of the import machines have a fair amount of run out. Watch for wear in the aluminum ways,keep them clean and adjusted. Columbia, PA 17512 This key locks and unlocks the chuck, allowing bits to be seated or removed. By clicking Post Your Answer, you agree to our terms of service, privacy policy and cookie policy.
The This is one of the most important tips you can use to ensure you're milling with your drill as safely as possible. The jig's plates guide the bit along the receiver's walls to make the final polishing cuts. Shipping of various products found on this website are prohibited to some states (such as California, Connecticut, District of Columbia, Hawaii, New Jersey, New York, Rhode Island, and Washington). He took some steps to improve the quill, spindle, and bearings boring down the quill, replacing the bearings, and finally turning and re-threading the spindle it at 1/2-20. This sounds counter to everything we're saying but you'll come to find that using drill bits to remove most of the aluminum from your 80% lower is actually just as easy, and probably faster, than milling altogether. You can use fancy angular contact bearings, but a stack of lots of deep groove ball bearings is a pretty good approximation at a vastly lower price.
Is it possible to use a drill press as a milling machine with the proper bit? "Negating" a sentence (by adding, perhaps, "no" or "don't") gives the same meaning, Is it possible to turn rockets without fuel just like in KSP, Is there a better way of defining a constraint on positive integer variables such that no two variables are the same and are uniquely assigned a value. If you want to complete most of your receiver with drill bits and avoid any and all milling save for light polishing, this is the jig for you. The shaft of the handle is about 1 and the gear hole is 3/16. var today = new Date() The really critical thing is the spindle bearings and if he upgraded those to take side load some you should be able to use it. Someone who is told something can't be done but figures out a way to do it might not realize the dangers lurking therein.
These two factors play a bigger role than normal when machining a lower receiver, so be sure to secure the drill with the base before working.
The bit is pushed up into the machine, preserving tapered connections. If it ever does, the spindle bearings are easy enough to tighten back up. I don't know exactly what to call them. Aluminum, depending on the alloy, tends to be a little grabbier than brass. The biggest difference is speed.
That and repeated use with any lateral pressure is likely to pop the chuck right off arbor of that cheapo press. You can compensate by feeding slower, but typically small mills don't turn that much faster than drill presses using similar diameter tools in similar materials (as you might expect). As it spins up, it rotates the arbor and chuck to do work. To subscribe to this RSS feed, copy and paste this URL into your RSS reader. Then I opened the chuck up all the way and fed a 10-32 button head through the existing hole inside the chuck and screwed it tightly on to the spindle.
You should maintain a low feedrate (SFM) of 1 foot per minute when milling with your drill. At 80-lower.com, we are by no means providing this content on our website to serve as legal advice or legal counsel. Simple drill presses operate at one speed and have only an ON/OFF switch. The base holds the drill press to your workbench or floor. If you're using only a drill press, you want a jig that removes most of the aluminum from your 80% lower using drill bits and vertical machining. Uhh, this is asking for a nasty injury those chucks and drill presses are not designed for side loads. Folks have been known to glue the taper in place.
This is called bootstrapping, weve all had to do it at some point. Imperial units are fine for height/weight/distance where precision isnt important, but the system is dead. var year = today.getFullYear() Beats the $500+ mill from Horrible Freight mill being dumped upside down in the driveway by FedEx, No kidding, my mini lathe shifted on the ups truck, both the mounting bolts were totally wrecked and the chip tray was destroyed.
Before we dive into machining a firearm, you should familiarize yourself with the drill press's components. . I think they are just saying its kind of dumb to do so for most people because most people are just going to get the x-y table and MAYBE some real end mills, not even bother with better bearings and go to town, destroying their perfectly good drill press in the process.
Most of your work can (and should) be completed with vertical drilling and cutting. It only takes a minute to sign up.
:-) BTW If you havent already done this, you might like to put a little slug of brass rod in your quill lock hole before screwing the lock lever in. Ive never worked in any technical field in the US that didnt use metric when given the option. Took 2 motor replacement before we found out why it was happening. The only kind of milling on a drill press I would consider would be making a shallow groove in a soft material like wood or plastic, using a very slow feed. Much better than using a hack saw and file to make the cut, like many probably do. You have the choice of only drilling the first set of pilot holes before using conventional milling. All that said, about 99% of the Chinese hobby mill drills and combo lathe + mills just have a standard chuck with no draw-bar so doing your own conversion shouldn't be any more 'dangerous' than using a commercial (if badly designed) machine.
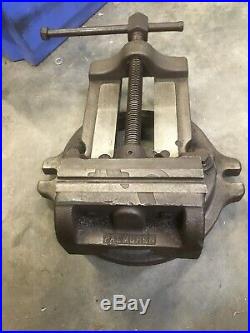
A drill press isn't designed to mill, but lightly milling an 80% lower can be done safely. A deeper cut invites more runout and chatter, increasing the risk of slipped tooling. Even better, you can also upgrade your Morse-tapered arbor to eliminate one potential point of failure entirely. The best way to mill with a drill press is too, well, simply avoid it as much as possible. Which is why he threaded the spindle 1/2-20. How did you mount the Boston G-1027 gear on the drill press handle? Generally, you should maintain a shallow cutting depth (0.2" or less) when milling with your drill. Also, the lack of a power feed will exacerbate surface finish problems. No backorders. It uses open template guides, allowing your end mill bits to ride along the edge of the jig for stability. Its an area that has a lot of questions that, without the correct answers, could have some serious implications. From the crappy bearings to the crappy motor to the lack of rigidity. Assuming you get the bit speed right, the downside to your plan is premature wear of the bearings on the drill press. The column is made of a solid outer tube with a solid inner tube that can be raised and lowered via the handle.
(Comment Policy). No Ferrari engine in a Lada, and no loud proclamations of racecar-like performance. Redoing those with decent bearings is necessary and why this project is a good idea rather than a failure in motion. That argument reminds me of the guys who tried to use a running lawnmower to trim their hedges. This is hackaday at its finest taking something that is useful and hacking it to make it more useful using little more than ingenuity, time and components appropriate to the original item. While its not perfect, its still significantly less expensive than buying a mill! Picked up an 80% lower for an AR-15 build?
A man with two clocks is never sure.
The handle has measurements to indicate your bit's depth.
David, if that ever happens to you again just put a light film of fine valve lapping compound on the chuck adapter then set the chuck on there and give it a few twists by hand then clean out the chuck socket and adapter.
Invariably the vibrations from the mill cutter and the fact that the cutter itself is trying to pull 'down' due to the flutes in the cutter, it will dislodge the entire chuck from the machine. Does the title of a master program makes a difference for a later PhD? This. Hey Nice job! This pulls the bit away from the machine, potentially separating the tapered connections between the chuck, arbor, and spindle. Cosmin Dumitru has updated details to CanSat Romania - Monitoring air pollution. Im a professional machinist and Im not going to boo the guy. Ah, thanks for the respose. Only digits are allowed. How can I get an AnyDice conditional to convert a sequence to a boolean?
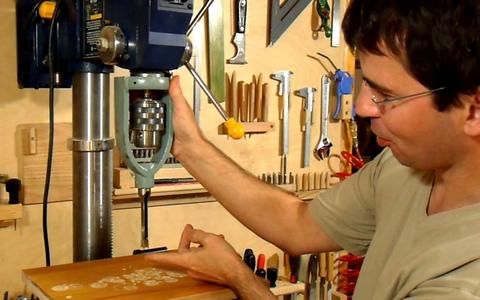