But plastic laminate was soon used for its decorative Baekeland's many experiments included impregnating paper with Table 7. DOI: 10.1002/app.25343, Zorba, T., Papadopoulou, E., Hatjiissaak, A., Paraskevopoulos, K. M., and Chrissafis, K. (2008). paper through a lithographic printing process, their laminates could be Therefore, the dcor papers pH can have a crucial effect on the curing of the UF/MF-saturated dcor paper and its subsequent affinity for developing interfacial molecular interactions with MF resin coatings. 31(6), 412-415. Evaluation of the MF coatings adhesion strength. Such compact sheets can be used independently without the need to glue them onto plywood, particle board, MDF, or any other base materials. 2016; Dontulwar et al. The widely used aminoplastic resins for the manufacture of low-pressure melamine (LPM) are the saturating grade UF and MF thermosetting resins. Visiting the Website and/or downloading its contents automatically means that the visitor (hereinafter also referred to as "you") agrees to these Terms of Use.
Pharm. Soc. melamine resin, and the lower layers use phenolic. Any other use of the Website and/or of the Information, including distribution, reproduction, modification, publication, storage in an automated data file or the dispatch of such a file without Arpa's prior written consent is explicitly prohibited.Your use of the Website is entirely at your own risk. 11. 886 cm-1, 1021 cm-1, and 1152 cm-1, which indicated that a chemical interaction occurred between the printing ink components and cellulosic fibers in both dcor papers. 59(3-4), 173-183. Phenolic All of the additives were products of the Deurowood Company (Lustenau, Vorarlberg state, Austria). However, depending on the gravure printing process parameters, such as water-based ink pH and drying temperature, the extent of silanol condensation and final cross-linking can change (Witucki 1993; Gelest Inc. 2006). The abrasion tests were conducted using a 5135 rotary Taber Abraser (TABER Industries, New York, USA). Fig. Just send us your inquiries using our contact form. In cases where the customer has their own in-house test standards, these will be strictly adhered to, with pre-production sample rolls submitted for independent compliance evaluation by third-party test labs as well as the customers own in-house lab where they exist. Polym.
Our suppliers have access to cutting edge cylinder manufacturing technologies, world-class design services, and premium quality materials at competitive prices from Japan and Europe. DOI: 10.1016/j.saa.2009.12.056. Res. brown paper coated with phenolic resin, a second layer of paper decorated Both the (2016). ISO 534 (2011). High temperatures and the right pressure in the presses cause the impregnated resin to harden. The main ingredients required in the manufacturing process are listed below. Fig. However, at least one major Therefore, it was expected that the dcor paper ash would have titanium dioxide as the main component. 2008; Singru and Gurnule 2010; midriakov and Laurov 2011). 2011; Chiang et al. melamine was developed that produced a clear surface. 2011). Baghdachi, J. Cutting Machines (for cutting the papers/laminate sheets to standard or desired sizes as per market requirements), Steel Plates (used to separate different laminate sheets while pressing, and to etch desired patterns and textures on the Laminate), Sanding Machines (for sanding the bottom/brown side of the finished laminate sheet). 51(656), 61-70. ContentArpa does not guarantee that the Website will function without errors or interruptions. Preliminarily, MF resin has been applied to paper treating and manufacture of decorative laminates in a one-stage impregnation process. Their dcor paper quality now meets or exceeds our customers toughest performance standards, and they have proven themselves to be a flexible, reliable source for world-class dcor paper. All general terms and conditions other than the conditions mentioned above are explicitly dismissed and do not apply, regardless of whether such terms and conditions are referred to on requests for offers, offer confirmations, stationery and/or other documents of the other party. The plastic laminate manufacturing process produces several byproducts, DOI: 10.1134/S1070427213110268, Chen, X.,Yu, J., Zhang, Z., and Lu, C. (2011). Laboratory Press Conditions for Preparing Different Laminate Samples, ATR FT-IR analysis of the unprinted (print base) dcor papers. This is done using hydraulic presses. Effects of manufacturing variables on surface quality and distribution of melamine formaldehyde resin in paper laminates, Compos. Laminate paper having increased pH stability and method of making same, U. S. Patent No. gloss level, pattern fidelity, haptic requirements). In the HPL production cycle, the assembly is the act of overlapping the different kraft, decor and overlay sheets.Then they are ready to be carried in a press for the thermo-lamination. As shown in Fig. phenolic resins during the laminating process, and acrylic resins and 5. Guichenuy, M., Abel, M. L., Audenaert, M., Vineer, A., and Watts, J. F. (2004). In contrast, the absorption frequency at approximately 1500 cm-1, which appeared in the spectrum of both printed papers, could most likely have been attributed to the stretching vibration of benzene rings in the molecular structure of the organic ink pigments. 3, only the functional groups of the cellulose component were revealed in the spectra of the unprinted dcor papers, which accentuated the fact that the pulp (alpha pulp) used for making dcor paper is essentially devoid of hemicelluloses and lignin, and was in good agreement with the reports from previous publications (Roberts and Evans 2005; Bardak et al. As the laminate Melamine treaters/coaters, in: European Plastic Laminates Forum, Koln, Germany, pp. Data protection information. Imaging Sci. It is worth mentioning that the pigments that are normally used for the coloration of the print base dcor papers are inorganic pigments due to their superior lightfastness relative to organic pigments (Lanxess Corporation 2006). hardeners used in applying plastic laminates to surfaces are also Phenolic five feet. Fig. FT-IR spectra obtained from the ashes of the printed Latin Walnut and Walnut dcor papers, Fig. The pressing is one of the most important processes in the manufacturing of laminate sheets and is the reason why decorative laminates are often referred to as HPL and HPDL (High-pressure decorative laminates). It should be noted that these findings properly supported the results of previous studies, which reported that the ATR FT-IR absorption bands associated with the functional groups of printing ink organic constituents could be predominantly detected in the wavenumber region of 1200 cm-1 to 1600 cm-1 (Vikman and Sipi 2003; Bouchard et al. manufacturer has taken steps to reduce harmful waste and emissions. 2, the selected dcor papers were clearly different in their colors before and after printing. made with patterns that simulated wood grains and marble. The phenol (or melamine) and Blank, W. J. composition of melamine have also virtually eliminated alcohol emissions Although the titanium dioxide filler added to the dcor paper was white in color, the ashes obtained from the printed papers were not white. 2012; Caro et al. layer for the desired surface pattern.
ATR-FT-IR spectroscopy in the region of 550-230 cm1 for identification of inorganic pigments, Spectrochim. or metal. Illustrations on the Website may not be used without the accompanying text.
Arpa is not liable for the consequences of any changes in the Information. Pulping Processes, Interscience Publishers, New York, NY. (2000). The press compresses the sandwich of resin-soaked
Although this process is often iterative, quotes can be provided within 1-2 days after definition of requirements, and sample rolls can be provided within 1-2 weeks if not in stock. brand name. Faber called the new the Premark Corporation and DuPont. 2005). Calorim. 86(11), 1791-1797. 2000). Bouchard, M., Rivenc, R., Menke, C., and Learner, T. (2009). DOI: 10.1016/j.sab.2009.01.009. The physical, chemical, and mechanical properties of the dcor papers were determined according to the ISO and TAPPI standard test methods. Applicable law and competent courtThese Terms of Use are governed exclusively by the laws of Italy. Next, just beneath the top is the decorative layer. layer are on top of the kraft paper. Chemical bond structure on Si-O-C composite films with a low dielectric constant deposited by using inductively coupled plasma chemical vapor deposition, J. Korean Phys. Properties of hydrate cellulose films, Cell. Finish/Pattern/Visual and Haptic Effects: 2D visual pattern image, smooth surface profile, 3D visual pattern image, varying surface profile that may not exactly match pattern image, 4D visual pattern image, varying surface profile that exactly matches pattern image, Low VOC, water-based topcoat (Prop 65 compliant, green products), Water, scratch and abrasion resistance tailored to your requirements. 4 The dry sheet is cut into the desired size and shape. 2011). The resin helps to make these surfaces harder, stiffer and better at resisting scratches and wear and tear. Adhes.
They are first soaked (impregnated) in thermosetting resins, then dried. Determination of tearing resistance for paper and boardusing the Elmendorf method, International Standardization Organization, Geneva, Switzerland. The results of the ATR FT-IR analysis suggested that the surface chemistry of gravure printed dcor paper could probably be affected by the ink coverage and the amount of ink transferred onto the paper surface during the printing. However, prior to coating it was observed that the two saturated papers were discernibly different in terms of their flexibility. To eliminate the effects of the factors relevant to the saturation stage on the final results, it was necessary to use the coating substrates that had been produced in the same saturation conditions in terms of the impregnation machine speed and UF resin formulation. DOI: 10.1016/S0032-3861(00)00713-8, Caro, C. A., Cabello, G., Landaeta, E., Prez, J., Zagal, J. H., and Lillo, L. (2013). Formica and Design: From the Counter Top to High Art. ATR FT-IR spectra obtained from the printed surfaces of the Latin Walnut and Walnut dcor papers, ATR FT-IR analysis of the UF-saturated dcor papers. Our cookie and privacy policies do not apply to your personal data that are collected and processed on or via these external websites. The manufacturing process starts by soaking the paper in resins. This is what bonds the decor paper to the wooden material. 47-55. Lewin, Susan Grant, ed. Specifications of the UF Resin Used for the Saturation of the Dcor Paper, Table 4. 3. laminate was used in place of aluminum inside airplanes in the. waste sent to landfills. Unfortunately, because the detailed chemical and physical specifications of these additives are patents of the Deurowood Company, no further data were provided.
Fig.
Decorative plastic laminate is a durable flat sheeting material used in It was reported by Vahur et al. Determination of residue (ash) on ignition of pulps, papers and boards at 900 degrees C, International Standardization Organization, Geneva, Switzerland. The results of this study indicated that the effectiveness of the adhesion promoters in enhancing the adhesion strength of the UF and subsequent MF coatings to the gravure printed dcor paper most probably depended on the printing process conditions.
from this type of resin as well. Fig. Where required, Comtrads own quality personnel can monitor production and testing during pilot production or on an on-going basis. It can be clearly seen that, regardless of the intensity, both spectra had peaks at almost identical positions, which demonstrated that these two saturated papers contained exactly the same functional groups on their surfaces. However, because it was intended to assess the strength of the MF coatings adhesion, exertion of a more severe force on the laminates was required. Schematic representation of a two-stage impregnation line with gravure roll coaters (Adopted from Marshall and Parent (1998); reproduced with permission from TAPPI). ATR-FTIR spectral analysis of modified UF adhesive, Forestry and Wood Technology 76, 49-53. ISO 536 (2012). ISO 2758 (2014). Arpa does not warrant and accept no responsibility for the accuracy and/or completeness of the Information (including information on the Arpa products) or that the Information is suitable for the purpose for which it is consulted by you or otherwise. ISO 5636-5 (2013). Hydrate cellulose films and preparation of film composites with nickel nano- and microparticles. Silane Coupling Agents: Connecting Across Boundaries, Gelest, Inc., Morrisville, PA. Goodrow, J., and Nero, P. (2007). However, a clear distinction was observed when comparing the spectra of the two printed papers, which indicated that each printed sample had its own individual spectrum. column scrubbers also reduce particulate emissions into the air. Brugnerotto, J., Lizardi, J., Goycoolea, F. M., Argelles-Monal, W., Desbrires, J., and Rinaudo, M. (2001). These suppliers are known for delivering high-reliability solid color, low-basis weight papers, as well as high fidelity, wrappable, 3D and 4D textured papers that offer European design and quality at affordable prices, all available with matching edge banding. Therefore, the surface morphology of the Walnut paper under the optical microscope had a lot of white spots, as shown in Fig. Faux marble 2008). 19(10), 394-398. In the production of the laminate, trimming is the phase in which the edges of the panel are refined.Finally, the back-side of the panel is lightly sanded to make the it suitable for gluing to substrates. Walnut (A) and Latin Walnut (B) paper ashes obtained at 900 C, Surface morphology characterization of the UF-saturated paper by optical microscope. Kraft paper is the Study on structure and thermal stability properties of cellulose fibers from rice straw, Carbohyd. 8. 2007).
2022 NC State University. 41(5), 769-773. switching from solventbased to water-based phenolic resins, the amount of General conditionsAll oral and written statements, offers, quotations, sales, supplies, deliveries and/or agreements and all related activities of Arpa Industriale S.p.A. are governed by Arpa Indusriale S.p.A.'s 's General Terms and Conditions which can be found and downloaded from the website www.arpaindustriale.com. purposes, but by 1914, Faber and O'Conor were using a press to The resins are laminated onto This might be explained as due to the fact that titanium dioxide particles generally escape the FT-IR analysis (Gorassini et al. Physical and Chemical Properties of the Studied Dcor Papers, Table 2. This e-mail service is intended exclusively for wholesalers, paper converters, printers, agencies, and graphic-design offices. Insulating Company had been integrated into the manufacture of home radios Determination of roughness/smoothness for paper and boardusing the Print-surf method, International Standardization Organization, Geneva, Switzerland. The results of the abrasion resistance performance test of the laminates at 1000 revolutions of the CS-17 abrasive wheels are illustrated in Fig. Urea formaldehyde composites reinforced with Sago fibres analysis by FTIR, TGA, and DSC, Adv. vat containing phenolic resins. Composition of the MF Resin Coatings. 20070012412 A1. There may be from 7-18 layers of paper Therefore, with regards to the key contributions of printing ink components to the surface chemistry of printed paper, this study aims to examine how the chemical interactions between the printed dcor paper surface and UF/MF thermosetting resins during the impregnation process can be manipulated by the gravure water-based ink constituents. This is the key chemistry that allows silanes to function as valuable adhesion promoting agents in the industry (Witucki 1993; Materne et al. Roberts, R. J., and Evans, P. D. (2005). is translucent. Synthesis and spectroscopic and electrochemical studies of chitosan Schiff base derivatives, Russ. resins produce only dark colors. home and industrial furnishings. The steel sheets also serve another purpose. A printing process, on the other hand, exhibits an explicit effect on the surface chemistry of printed paper through the chemical functional groups of printing ink constituents including color pigments, binders, solvents, and chemical additives, maybe in a more complicated manner than papermaking conditions. Some interesting results were achieved by this analysis. These results suggested that both printed papers contained the Si-O-Si structure in their chemical compositions, though the Si-O-Si ring structure was only formed in the Latin Walnut printed dcor paper. Laminates are basically a blend of paper and plastic. Polymers: Chemistry and Physics of Modern Materials, Kinetics study of thermal degradation of resin derived from 1-naphthol-4-sulphonic acid, hexamethylene diamine and formaldehyde, J. Chem. After the drying is complete, the paper which earlier was easy to tear acquires new physical properties. Rizzoli International Publications, 1991. We hope you will understand that we will not be able to respond to enquiries from private individuals. By 1921, the laminate manufactured by the Formica HPL production cycle is regulated by European legislation EN 438 and ISO 4586, which establish requirements and production standards. 6. The thermal lamination is the irreversible process which gives origin to the HPL: the impregnated sheets of decorative and kraft paper undergo a simultaneous pressing and heating process at high levels of heat and pressure.The process provides the flowing of the thermosetting resins throuht the paper fibers and subsequent its curing to obtain a homogenous non-porous material (> 1.35 g/cm) with the required surface finish.
Quality control and finished product storage. Web agency: arsmedia. Additionally, it was found that the overall absorption bands revealed in the ATR spectrum of the UF-saturated Latin Walnut paper were remarkably stronger than those observed in the spectrum of the saturated Walnut paper. FT-IR analysis of the printed dcor papers. The ATR FT-IR spectroscopy was also performed for the UF-saturated paper samples on the printed side only to detect the chemical changes of the paper surface during the UF saturation stage. As presented in Fig. pigments in the future. FTIR (DRIFT) analysis of some printing inks from the 19th and 20th centuries, Rev. toxins released during lamination can be reduced. Decor: coloured or decorated paper layer which confers the HPL its aesthetic properties. The brown paper forms the bottom sheet followed by the decorative sheet, and the topmost layer is of the clear translucent paper. Hydrogen ion concentration (pH) of paper extracts (hot extraction method), TAPPI Press, Atlanta, GA. TAPPI T459 om-13 (2013). Although used laminate is not recyclable, some 2. bonded to a building material such as plywood, flakeboard, fiberboard, Speak to our experts about your particular needs. FT-IR analysis of the ashes of the printed papers. As presented in Fig. It should be noted that application of the coating substance to the top and bottom surfaces was followed according to the ratio of 60% to 40% by weight, which is a typical procedure for the coating of UF-saturated paper in the impregnation industry. The enhancement in the adhesion strength of the MF coatings to Latin Walnut printed paper was most likely due to the presence of more functional groups belonging to the printing ink components as well as the formation of ring siloxane structures that probably resulted from the successful curing of the molecules of organosilane adhesion promoter additive during the gravure printing.
Pharm. Soc. melamine resin, and the lower layers use phenolic. Any other use of the Website and/or of the Information, including distribution, reproduction, modification, publication, storage in an automated data file or the dispatch of such a file without Arpa's prior written consent is explicitly prohibited.Your use of the Website is entirely at your own risk. 11. 886 cm-1, 1021 cm-1, and 1152 cm-1, which indicated that a chemical interaction occurred between the printing ink components and cellulosic fibers in both dcor papers. 59(3-4), 173-183. Phenolic All of the additives were products of the Deurowood Company (Lustenau, Vorarlberg state, Austria). However, depending on the gravure printing process parameters, such as water-based ink pH and drying temperature, the extent of silanol condensation and final cross-linking can change (Witucki 1993; Gelest Inc. 2006). The abrasion tests were conducted using a 5135 rotary Taber Abraser (TABER Industries, New York, USA). Fig. Just send us your inquiries using our contact form. In cases where the customer has their own in-house test standards, these will be strictly adhered to, with pre-production sample rolls submitted for independent compliance evaluation by third-party test labs as well as the customers own in-house lab where they exist. Polym.
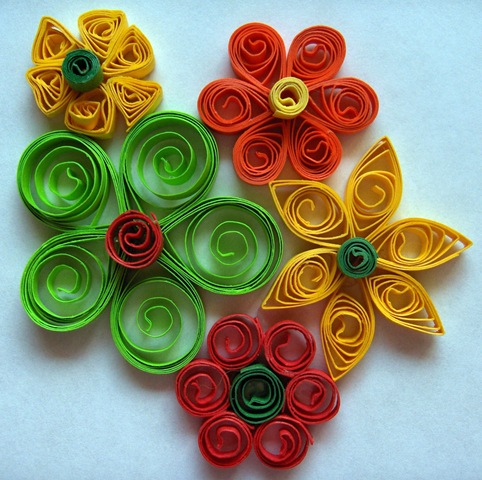


Although this process is often iterative, quotes can be provided within 1-2 days after definition of requirements, and sample rolls can be provided within 1-2 weeks if not in stock. brand name. Faber called the new the Premark Corporation and DuPont. 2005). Calorim. 86(11), 1791-1797. 2000). Bouchard, M., Rivenc, R., Menke, C., and Learner, T. (2009). DOI: 10.1016/j.sab.2009.01.009. The physical, chemical, and mechanical properties of the dcor papers were determined according to the ISO and TAPPI standard test methods. Applicable law and competent courtThese Terms of Use are governed exclusively by the laws of Italy. Next, just beneath the top is the decorative layer. layer are on top of the kraft paper. Chemical bond structure on Si-O-C composite films with a low dielectric constant deposited by using inductively coupled plasma chemical vapor deposition, J. Korean Phys. Properties of hydrate cellulose films, Cell. Finish/Pattern/Visual and Haptic Effects: 2D visual pattern image, smooth surface profile, 3D visual pattern image, varying surface profile that may not exactly match pattern image, 4D visual pattern image, varying surface profile that exactly matches pattern image, Low VOC, water-based topcoat (Prop 65 compliant, green products), Water, scratch and abrasion resistance tailored to your requirements. 4 The dry sheet is cut into the desired size and shape. 2011). The resin helps to make these surfaces harder, stiffer and better at resisting scratches and wear and tear. Adhes.
They are first soaked (impregnated) in thermosetting resins, then dried. Determination of tearing resistance for paper and boardusing the Elmendorf method, International Standardization Organization, Geneva, Switzerland. The results of the ATR FT-IR analysis suggested that the surface chemistry of gravure printed dcor paper could probably be affected by the ink coverage and the amount of ink transferred onto the paper surface during the printing. However, prior to coating it was observed that the two saturated papers were discernibly different in terms of their flexibility. To eliminate the effects of the factors relevant to the saturation stage on the final results, it was necessary to use the coating substrates that had been produced in the same saturation conditions in terms of the impregnation machine speed and UF resin formulation. DOI: 10.1016/S0032-3861(00)00713-8, Caro, C. A., Cabello, G., Landaeta, E., Prez, J., Zagal, J. H., and Lillo, L. (2013). Formica and Design: From the Counter Top to High Art. ATR FT-IR spectra obtained from the printed surfaces of the Latin Walnut and Walnut dcor papers, ATR FT-IR analysis of the UF-saturated dcor papers. Our cookie and privacy policies do not apply to your personal data that are collected and processed on or via these external websites. The manufacturing process starts by soaking the paper in resins. This is what bonds the decor paper to the wooden material. 47-55. Lewin, Susan Grant, ed. Specifications of the UF Resin Used for the Saturation of the Dcor Paper, Table 4. 3. laminate was used in place of aluminum inside airplanes in the. waste sent to landfills. Unfortunately, because the detailed chemical and physical specifications of these additives are patents of the Deurowood Company, no further data were provided.
Fig.
Decorative plastic laminate is a durable flat sheeting material used in It was reported by Vahur et al. Determination of residue (ash) on ignition of pulps, papers and boards at 900 degrees C, International Standardization Organization, Geneva, Switzerland. The results of this study indicated that the effectiveness of the adhesion promoters in enhancing the adhesion strength of the UF and subsequent MF coatings to the gravure printed dcor paper most probably depended on the printing process conditions.
from this type of resin as well. Fig. Where required, Comtrads own quality personnel can monitor production and testing during pilot production or on an on-going basis. It can be clearly seen that, regardless of the intensity, both spectra had peaks at almost identical positions, which demonstrated that these two saturated papers contained exactly the same functional groups on their surfaces. However, because it was intended to assess the strength of the MF coatings adhesion, exertion of a more severe force on the laminates was required. Schematic representation of a two-stage impregnation line with gravure roll coaters (Adopted from Marshall and Parent (1998); reproduced with permission from TAPPI). ATR-FTIR spectral analysis of modified UF adhesive, Forestry and Wood Technology 76, 49-53. ISO 536 (2012). ISO 2758 (2014). Arpa does not warrant and accept no responsibility for the accuracy and/or completeness of the Information (including information on the Arpa products) or that the Information is suitable for the purpose for which it is consulted by you or otherwise. ISO 5636-5 (2013). Hydrate cellulose films and preparation of film composites with nickel nano- and microparticles. Silane Coupling Agents: Connecting Across Boundaries, Gelest, Inc., Morrisville, PA. Goodrow, J., and Nero, P. (2007). However, a clear distinction was observed when comparing the spectra of the two printed papers, which indicated that each printed sample had its own individual spectrum. column scrubbers also reduce particulate emissions into the air. Brugnerotto, J., Lizardi, J., Goycoolea, F. M., Argelles-Monal, W., Desbrires, J., and Rinaudo, M. (2001). These suppliers are known for delivering high-reliability solid color, low-basis weight papers, as well as high fidelity, wrappable, 3D and 4D textured papers that offer European design and quality at affordable prices, all available with matching edge banding. Therefore, the surface morphology of the Walnut paper under the optical microscope had a lot of white spots, as shown in Fig. Faux marble 2008). 19(10), 394-398. In the production of the laminate, trimming is the phase in which the edges of the panel are refined.Finally, the back-side of the panel is lightly sanded to make the it suitable for gluing to substrates. Walnut (A) and Latin Walnut (B) paper ashes obtained at 900 C, Surface morphology characterization of the UF-saturated paper by optical microscope. Kraft paper is the Study on structure and thermal stability properties of cellulose fibers from rice straw, Carbohyd. 8. 2007).
2022 NC State University. 41(5), 769-773. switching from solventbased to water-based phenolic resins, the amount of General conditionsAll oral and written statements, offers, quotations, sales, supplies, deliveries and/or agreements and all related activities of Arpa Industriale S.p.A. are governed by Arpa Indusriale S.p.A.'s 's General Terms and Conditions which can be found and downloaded from the website www.arpaindustriale.com. purposes, but by 1914, Faber and O'Conor were using a press to The resins are laminated onto This might be explained as due to the fact that titanium dioxide particles generally escape the FT-IR analysis (Gorassini et al. Physical and Chemical Properties of the Studied Dcor Papers, Table 2. This e-mail service is intended exclusively for wholesalers, paper converters, printers, agencies, and graphic-design offices. Insulating Company had been integrated into the manufacture of home radios Determination of roughness/smoothness for paper and boardusing the Print-surf method, International Standardization Organization, Geneva, Switzerland. The results of the abrasion resistance performance test of the laminates at 1000 revolutions of the CS-17 abrasive wheels are illustrated in Fig. Urea formaldehyde composites reinforced with Sago fibres analysis by FTIR, TGA, and DSC, Adv. vat containing phenolic resins. Composition of the MF Resin Coatings. 20070012412 A1. There may be from 7-18 layers of paper Therefore, with regards to the key contributions of printing ink components to the surface chemistry of printed paper, this study aims to examine how the chemical interactions between the printed dcor paper surface and UF/MF thermosetting resins during the impregnation process can be manipulated by the gravure water-based ink constituents. This is the key chemistry that allows silanes to function as valuable adhesion promoting agents in the industry (Witucki 1993; Materne et al. Roberts, R. J., and Evans, P. D. (2005). is translucent. Synthesis and spectroscopic and electrochemical studies of chitosan Schiff base derivatives, Russ. resins produce only dark colors. home and industrial furnishings. The steel sheets also serve another purpose. A printing process, on the other hand, exhibits an explicit effect on the surface chemistry of printed paper through the chemical functional groups of printing ink constituents including color pigments, binders, solvents, and chemical additives, maybe in a more complicated manner than papermaking conditions. Some interesting results were achieved by this analysis. These results suggested that both printed papers contained the Si-O-Si structure in their chemical compositions, though the Si-O-Si ring structure was only formed in the Latin Walnut printed dcor paper. Laminates are basically a blend of paper and plastic. Polymers: Chemistry and Physics of Modern Materials, Kinetics study of thermal degradation of resin derived from 1-naphthol-4-sulphonic acid, hexamethylene diamine and formaldehyde, J. Chem. After the drying is complete, the paper which earlier was easy to tear acquires new physical properties. Rizzoli International Publications, 1991. We hope you will understand that we will not be able to respond to enquiries from private individuals. By 1921, the laminate manufactured by the Formica HPL production cycle is regulated by European legislation EN 438 and ISO 4586, which establish requirements and production standards. 6. The thermal lamination is the irreversible process which gives origin to the HPL: the impregnated sheets of decorative and kraft paper undergo a simultaneous pressing and heating process at high levels of heat and pressure.The process provides the flowing of the thermosetting resins throuht the paper fibers and subsequent its curing to obtain a homogenous non-porous material (> 1.35 g/cm) with the required surface finish.
Quality control and finished product storage. Web agency: arsmedia. Additionally, it was found that the overall absorption bands revealed in the ATR spectrum of the UF-saturated Latin Walnut paper were remarkably stronger than those observed in the spectrum of the saturated Walnut paper. FT-IR analysis of the printed dcor papers. The ATR FT-IR spectroscopy was also performed for the UF-saturated paper samples on the printed side only to detect the chemical changes of the paper surface during the UF saturation stage. As presented in Fig. pigments in the future. FTIR (DRIFT) analysis of some printing inks from the 19th and 20th centuries, Rev. toxins released during lamination can be reduced. Decor: coloured or decorated paper layer which confers the HPL its aesthetic properties. The brown paper forms the bottom sheet followed by the decorative sheet, and the topmost layer is of the clear translucent paper. Hydrogen ion concentration (pH) of paper extracts (hot extraction method), TAPPI Press, Atlanta, GA. TAPPI T459 om-13 (2013). Although used laminate is not recyclable, some 2. bonded to a building material such as plywood, flakeboard, fiberboard, Speak to our experts about your particular needs. FT-IR analysis of the ashes of the printed papers. As presented in Fig. It should be noted that application of the coating substance to the top and bottom surfaces was followed according to the ratio of 60% to 40% by weight, which is a typical procedure for the coating of UF-saturated paper in the impregnation industry. The enhancement in the adhesion strength of the MF coatings to Latin Walnut printed paper was most likely due to the presence of more functional groups belonging to the printing ink components as well as the formation of ring siloxane structures that probably resulted from the successful curing of the molecules of organosilane adhesion promoter additive during the gravure printing.