The physical dimensions of its structure, as shown below, does not allow boundary layers to grow and introduce enhanced mixing through eddies and turbulence.
As advances in epoxy and silicone materials constantly evolve, manufacturers of advanced electronic systems will find that Download Now, 29julAll Day30International Conference on Advanced Vehicle Thermal Management Technologies, International Conference on Advanced Vehicle Thermal Management Technologies aims to bring together leading academic scientists, researchers, and research scholars to exchange and share their experiences and research results on all. ERG has a 50-year history of making quality Duocel material, is certified to AS9100 Rev D, and is vertically integrated with a focus on customer service and turning ideas into production parts. Advanced Packaging Laboratory at East Fishkill, NY. Method of manufacturing of RMS heat exchangers depends on the material and the design. Figure 5. Figure 2. Produced by Electronic Cooling, it showcases the newest techniques and products in the industry.
This positions Duocel as a great design choice for high performance applications.
heat metal foam exchangers sinks feasibility matrix composites Figure 2 shows aluminum foam-based articles made by vacuum brazing [6]. Since the thermal conductivity is a vector quantity, its value will be a function of not just the amount of compression (as it is for the effective surface area), but also of the direction of compression. The effective thermal conductivity of 6061 Al based foams biaxially increases to ~ 30 W/m-K when unidirectionally compressed in X direction to 50% relative density in the (YZ) plane where ligaments are aligned in Y and Z directions. The open cell structure of RMF allows cleaning of any residual salts left over from the dip brazing bath. The heat exchangers were tested by exposing their outer surface to combustion gases at a temperature of 550C and 750C while being cooled by air flowing through them at room temperature at velocities up to 5 m/s.
The effective film coefficient is proportional to the density. Duocel works especially well when heat exchanger designs call for conformal shapes, high heat fluxes, and/or volumetric constraints.
A 2.54cm x 2.54cm (1.00x1.00) resistor was eutectic Sn/Pb soldered on the center of the Cu Plate in inert gas environment. Distribution of differential pressure (top) and the surface temperature of the cold plate built with 30 ppi and 30% Cu RMF Foam at 1 GPM flow rate. ERG has decades of experience, engineering expertise, and design data for everything necessary to model, prototype, and manufacture complete heat exchanger systems.
18 (Tuesday) 9:00 am - 19 (Wednesday) 5:00 pm, About Us | Subscribe | Advertise | Contribute | Contact UsCopyright 2022 Lectrix.
(or is it just me), Smithsonian Privacy As with other foam based designs, the ability to manufacture conformal PCM heat exchangers allows them to be used on components that traditionally have had to utilize sub-optimal cooling methods. Focused on Thermal Management, TIMs, Fans, Heat Sinks, CFD Software, LEDs/Lighting, June 14, 2018 Burhan Ozmat Aerospace, Articles, Automotive, Communications, Computer, Consumer, Data Centers, Defense, Electronics Cooling Blog, Featured, Heat Exchanger, Industrial, IT Products, Medical, Power, Research, TECs. Experimental Study of Thermal Performance: The test module was fabricated by inert atmosphere brazing a 2.54cm x 2.54cm x 0.635cm (1.00 x 1.00 x 0.250) Cu block to the center of a 5.08cm x 5.08cm x 0.318cm (2.00 x 2.00 x 0.125 thick) Cu. Duocel foam can elevate a heat exchanger design by utilizing the high surface area and high thermal conductivity of the foam structure to enhance the overall heat transfer of a system, all within a compact and lightweight form factor. heat graphite sink pcm foam diode laser bond sinks bonding paraffin packages phase joined materials change cored figure Phase Change Material (PCM) Heat ExchangersPCM heat exchangers work exceptionally well for high heat flux, short duration events, as well as space-based cooling applications where air is not available to cool the system.
exchanger [1] Ashby, M. F. et al.
The net outcome is enhanced heat transfer due to high local film coefficients. Heat shields were made by depositing porous skins on metal foam and it was observed that a small amount of coolant leaking through the pores notably reduces the heat transfer from the hot gases. The temperature rise of the air, the surface temperature of the heat exchangers and the air temperature inside the heat exchanger were measured. The foams high surface area to volume ratio and ligament structure interrupts boundary layers, creating turbulent flow and enhanced mixing, resulting in higher heat transfer compared to conventional technologies. A Plexiglas housing of the same cavity depth was fabricated out of a 0.635cm (0.250) thick Plexiglass sheet and screwed to the Al and Cu plates with cork gasket. degrees from Technical University of Istanbul. Thermische Performance elektronischer Gerte, 2022 by COMSOL. The results of such tests agree with the results of the calculations as presented in Figure 3. Materials, Compounds, Adhesives, Substrates.
Flow and the thermal resistances of Cu foam based Cold plates [6]. prous ecplaza A foam based heat exchanger is a compact and highly efficient technology that transfers heat between two or more fluids in order to control the thermal performance of critical components in a system. Notice that the cross sections of roughly 2 mm long solid ligaments are mostly triangular. The average effective film coefficient may be estimated from the measured power input to the resistant heater, and the difference between the average temperatures of the coolant and the resistor as was done in authors laboratory. porous aluminium metal heat aluminum foam sintered exchanger mufflers material conductivity thermal manufacturer vs manufacturing filter The thickness (similar to fin efficiency), Thermo-physical properties of the coolant. The estimated local film coefficient of 1 W/cm20C for 63 cm3 /sec (1 GPM) flow rate was used in generating the thermal performance surfaces shown in Figure 3 [2]. HXs with exposed RMF can be fabricated by either dip brazing or vacuum brazing. COMSOL Multiphysics has been used to reproduce experimental data and generate an optimized geometry to maximize the heat flux. The model was generated taking advantage of Brinkman Equations interface for porous media.
[3] Brunauer, Emmet, Teller, Journal of the American Chemical Society, Volume 60, 1938, p 309. The flow rate and the inlet temperature of the inlet DI water were kept constant using a recirculating chiller. Where: , the proportionality constant = 0.346, kb , the thermal conductivity of the base material, , the porosity (relative density) of as foamed RMF ~ 8%. A high power electric heater was used to produce hot air at 300C that passed over the foam heat exchanger while the cooling air was blown through it. heat exchanger copper tube foam metal exchange Both radiation and convective heat transfer phenomena have been taken into account, adopting a multiphysics approach. Metal foam can be applied to all types of heat exchangers as an alternative to traditional fins or microchannels.
T may be calculated by Equation (3) where w=1000 (kg/m3 ), V= 6.3*10-5 m3 /sec (1.0 GPM), CPW=4184 (J/kg-o C), Tin=21o C, and the maximum allowed surface temperature of the cooled electronic device TMax=60o C. Rth and Pressure Drop Measurements and Calculations: Rth was calculated using the above procedure. The mostly triangular cross section and only a couple of millimeter long ligament geometry of RMF offers significant advantages in convective cooling.
5, pp. Essentially all of the liquid single- and two-phase heat exchangers that ERG designs take advantage of compressed Duocel foam in order to maximize performance in a small volume. The thickness range for both the Al and Cu foams is 0-38 mm. metal foam energy absorbers erg aerospace corporation materials announcement
Al RMF based HXs can be fabricated with vacuum or dip brazing.
csmonitor The thermal conductivity of 6061 Al and C10100 Cu, most common RMF materials, are about 170 W/m-K and 390 W/m-K, respectively. boiler exchanger geometrical foams convective The s of RMF was characterized using experimental measurements, by multipoint Brunauer, Emmett and Teller (BET) method by adsorption of krypton gas at 77.4 K, and the modelling studies by authors. Figure 5. 40 pores per inch (PPI) 6101 Al based metal foam consisting of nodes and ligaments forming a space filling network of dodecahedrons with 12 pentagon shaped facets. Distilled water at 1 GPM flow rate was used as the coolant for generating the thermal performance surfaces shown in Figure 3 [2]. The foam conductivity has been computed according to a formula wildly adopted in literature. Drawing of the Cu RMF Cold Plate, Figure 6. Foam based heat exchangers (typically aluminum or copper foams) operate on the same fundamentals as all heat exchangers, but with increased surface area and turbulent flow to maximize heat transfer, resulting in better performance in a smaller package. 18oct(oct 18)9:00 am19(oct 19)5:00 pmFeaturedVirtual EventThermal LIVE Fall 2022. Required fields are marked *, Sponsored byMaster Bond 12 -16., Sept. 1996. Topics include new methods in liquid cooling, unique TIMs, connector selection, and much more. Since the CTE mismatch related thermal stresses and deformations are limited, the reliability of the integral heat exchanger, and the thermal base is not compromised, as verified by several hundreds of thermal cycles [5]. Thermal performance of RMF Heat Exchangers: The major factors scaling the thermal performance of RMF HX are: The recommended liquid coolants are distilled (DI)water, ethylene glycol, jet fuel, lubricating motor oils, Castrol, inert fluoro-carbons etc. With data-driven internal CFD models, the Duocel structure can be customized to maximize performance in a given volume. Heat transfer measurements were performed on a test rig capable of generating hot gas up to 1000C. Nickel foam sheets with pore densities of 10 and 40 pores per linear inch (PPI), have been used to make the heat exchangers and heat shields by using thermal spray coating to deposit an Inconel skin on a foam core. The fabrication of Cu foam-based heat exchangers where Cu foam is bonded to a Cu plate of enclosed housing are fabricated with inert-atmosphere, high-temperature brazing or vacuum brazing furnaces with suitable Cu-Ag solid braze preforms. Figure 8 depicts the results of CFD analyses for a cold plate built with 30 ppi, 30% dense Cu foam. heat exchanger thermal transfer multiple plate exchangers The experimental results are found to be in good agreement with the predicted values of the model.
The 3D structure of Duocel foam acts as a matrix to enhance the conductivity of the PCM (typically a paraffin wax), resulting in a more complete transfer of heat into the PCM. Heat transfer though open-cell metal foam is experimentally studied for heat exchanger and heat shield applications at high temperatures (750C). The vertical axis is the effective flat plate film coefficient whereas the X and Y axis of the surface plot show the thickness and the density of RMF, respectively.
The structural and thermal characteristics of RMF foams also offers similar advantages in passive phase change and two-phase flow applications. Pressure drop measurements were also performed for 10 and 40PPI metal foam. Thermal Interfaces and Convective Film Coefficients: An RMF based compact heat exchanger can be integrated to the sources of heat generation via solder bonding. Thermal conductivity of the base material (Al, Cu, Ag or others). [5] Final Program Report, COMNAVSEASYSCOM contract N00024-94-NR58001. [2] B. Ozmat et al., Thermal Applications of Open Cell Metal Foams Materials and Manufacturing Processes, Special Edition, Vol.19, No.
Studies show that RMF Based CP and HXs offer high thermal performance due to their extremely high specific surface area, local film coefficients and thermal conductivity particularly for lower volume and weight applications. iieta exchanger entropy Produced by Electronic Cooling. The structures enhanced mixing makes it a great choice for two-phase flow applications.
Double and single sided see through functional cold plates (left), top view of the single sided test unit (right). The ranges of effective heat transfer coefficient for the Al and Cu foams are 0 to 7.5 (W/cm2 o C) and 0 to 15 (W/cm2 o C), respectively.
desiccant sensible latent exchanger Use, Smithsonian Integration eliminates the highly resistive thermal interfaces of soft materials such as thermal pads, pastes or thermal epoxies commonly used to couple discrete devices, Hybrid Multi-Chip Modules (HMCM) of photonic and electronic devices to cold plates.
His main field is Mechanical and Thermal behavior of engineering materials where
Effective film coefficients and surface area density of 30 ppi, 30% dense Al RMF were input to CFD using a proprietary method, to calculate the thermal and flow resistance of the test cold plate. exchangers foams rmf reticulated foam heat metal regasification exchangers application gas performance natural system metal foam matrix heat open cellular structures sinks feasibility composites exchangers celled periodic schematic representations close figure heat porous aluminium aluminum surface area material metal volumes pore exchangers thermal conductivity transfer exchanger In the early stages of design, the feasibility of a given cold plate technology may be assessed by its thermal resistance (Rth) which is commonly calculated by Equation (2). 6-20, 2000. Figure 7. steam air heat exchanger recovery customize fins larger paper drying Your internet explorer is in compatibility mode and may not be displaying the website correctly.
An RMF may be brazed to low expansion skin layers and function as a constraining doublesided core heat exchanger (HX) for printed wiring boards (PWBs). Heat SinksDuocel heat sinks are often thinner than standard fins, reducing the overall height by 66% of the heat exchanger. To optimize the Duocel structure, ERG customizes the base material (primarily high conductivity metals like aluminum and copper), the pore size (smaller pores like a 40 PPI foam equates to higher surface area to volume ratio), and the ligament size (~8% relative density provides a good conduction path for the heat into the cooling fluid)..
Agreement NNX16AC86A, Is ADS down?
foam nickel
Figure 1.
There are quite a few ways to fabricate RMF [1], however the investment casting method of manufacturing produces the most desirable material properties. Thermal LIVE 2022 is a two-day, free online learning and networking event for electronics and mechanical engineers to learn about the latest topics in thermal management. Solder pastes may be used to fabricate CPs in inert-atmosphere furnaces where RMF is exposed. listed if standards is not an option). Thermographic measurements were done on 40PPI foam heat exchangers using a high temperature infrared camera. These features result in a high local film coefficient. The cold plate performance requirement for a high-power electronics device is defined by the thermal resistance. The effective bulk thermal conductivity however, depends on the porosity of the foam RMFs effective bulk conductivity (ke) may be estimated by Equation (1) [2]. The geometry of RMF cell structure and the high purity and ductility of its metal produce the most desirable characteristics for heat exchanger (HX) applications. One additional factor to enhance heat transfer that is unique to Duocel metal foam is the ability to compress the material by a factor of up to 6x. Figure 4. RFMs demonstrate compatibility with a wide range of liquids and gaseous coolants which makes the technology advantageously suitable for a wide range of commercial and military applications. The effective bulk conductivity of 8% dense 6061 Al RMF is about 4.7 W/m-K. Due to their high ductility, RMFs can undergo significant inelastic and elastic buckling deformations without failure of the ligaments, resulting in an increase in the relative density of the foam structure up to 50%.
Specifically, the value of Rth at V= 6.3*10-5 m3 /sec (1.0 GPM) is equal to 0.042o C/W. Burhan Ozmat received his Ph.D. degree from Massachusetts Institute of Technology as a DOE fellow, MSc and BSc
RMFs are compatible with DI water, inert fluoro-carbons, jet fuel, and inert gases. The important parameters of the RMFs are; thermal conductivity, heat transfer surface area, high mechanical ductility and compliance. The short answer is that Duocel Foam can be applied to any type of heat exchanger. Pictures and drawing of the cold plate are depicted in Figures 4 and 5 respectively. Your email address will not be published. based advanced thermal technology products.
exchanger heat Figure 8.
Metal foams are innovative lightweight materials with unique heat dissipation properties. Local Thermal Equilibrium approach has been used.
3, pp. Duocel foam cores can be machined and brazed into housings, creating an exceptional thermal interface and simplifying the overall system complexity which results in higher quality and more repeatable parts. Alle Rechte vorbehalten. Pore size measured as PPI, the linear density of pores per inch (5-40 ppi). Notice, Smithsonian Terms of An analytical model was developed based assuming local thermal non-equilibrium that accounts for the temperature difference between solid and fluid phase. One of the most important features of the RMFs is their extremely high and scalable surface area density (s ) compare to those of brazed or extruded fins and fin pins. Figure 3. The foam manufacturing process preserves the high purity of the material in the RMF.
exchanger cooling foam heat dry metal The volume flow rate, inlet and exit temperature of the coolant were monitored via flow meters and thermocouples. The solid ligament structure allows for ductile compression to increase surface area; most other metal foams have hollow ligaments, or have a buildup of layers that prevent ductile compression.
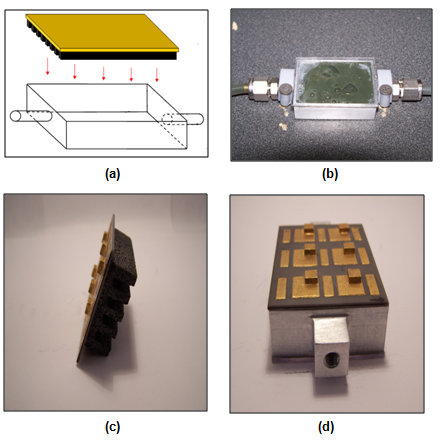


The effective film coefficient is proportional to the density. Duocel works especially well when heat exchanger designs call for conformal shapes, high heat fluxes, and/or volumetric constraints.






[3] Brunauer, Emmet, Teller, Journal of the American Chemical Society, Volume 60, 1938, p 309. The flow rate and the inlet temperature of the inlet DI water were kept constant using a recirculating chiller. Where: , the proportionality constant = 0.346, kb , the thermal conductivity of the base material, , the porosity (relative density) of as foamed RMF ~ 8%. A high power electric heater was used to produce hot air at 300C that passed over the foam heat exchanger while the cooling air was blown through it. heat exchanger copper tube foam metal exchange Both radiation and convective heat transfer phenomena have been taken into account, adopting a multiphysics approach. Metal foam can be applied to all types of heat exchangers as an alternative to traditional fins or microchannels.



csmonitor The thermal conductivity of 6061 Al and C10100 Cu, most common RMF materials, are about 170 W/m-K and 390 W/m-K, respectively. boiler exchanger geometrical foams convective The s of RMF was characterized using experimental measurements, by multipoint Brunauer, Emmett and Teller (BET) method by adsorption of krypton gas at 77.4 K, and the modelling studies by authors. Figure 5. 40 pores per inch (PPI) 6101 Al based metal foam consisting of nodes and ligaments forming a space filling network of dodecahedrons with 12 pentagon shaped facets. Distilled water at 1 GPM flow rate was used as the coolant for generating the thermal performance surfaces shown in Figure 3 [2]. The foam conductivity has been computed according to a formula wildly adopted in literature. Drawing of the Cu RMF Cold Plate, Figure 6. Foam based heat exchangers (typically aluminum or copper foams) operate on the same fundamentals as all heat exchangers, but with increased surface area and turbulent flow to maximize heat transfer, resulting in better performance in a smaller package. 18oct(oct 18)9:00 am19(oct 19)5:00 pmFeaturedVirtual EventThermal LIVE Fall 2022. Required fields are marked *, Sponsored byMaster Bond 12 -16., Sept. 1996. Topics include new methods in liquid cooling, unique TIMs, connector selection, and much more. Since the CTE mismatch related thermal stresses and deformations are limited, the reliability of the integral heat exchanger, and the thermal base is not compromised, as verified by several hundreds of thermal cycles [5]. Thermal performance of RMF Heat Exchangers: The major factors scaling the thermal performance of RMF HX are: The recommended liquid coolants are distilled (DI)water, ethylene glycol, jet fuel, lubricating motor oils, Castrol, inert fluoro-carbons etc. With data-driven internal CFD models, the Duocel structure can be customized to maximize performance in a given volume. Heat transfer measurements were performed on a test rig capable of generating hot gas up to 1000C. Nickel foam sheets with pore densities of 10 and 40 pores per linear inch (PPI), have been used to make the heat exchangers and heat shields by using thermal spray coating to deposit an Inconel skin on a foam core. The fabrication of Cu foam-based heat exchangers where Cu foam is bonded to a Cu plate of enclosed housing are fabricated with inert-atmosphere, high-temperature brazing or vacuum brazing furnaces with suitable Cu-Ag solid braze preforms. Figure 8 depicts the results of CFD analyses for a cold plate built with 30 ppi, 30% dense Cu foam. heat exchanger thermal transfer multiple plate exchangers The experimental results are found to be in good agreement with the predicted values of the model.





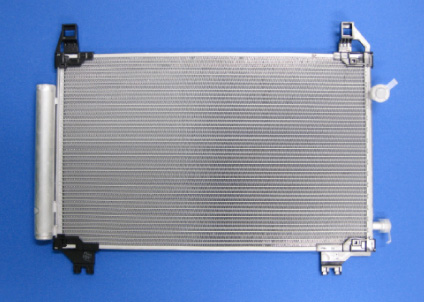



/is2.ecplaza.com/ecplaza1/offers/b/ba/bae/1140614750/copper-foamcu-foamprous.jpg)


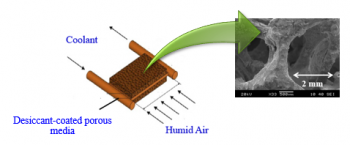

Metal foams are innovative lightweight materials with unique heat dissipation properties. Local Thermal Equilibrium approach has been used.
3, pp. Duocel foam cores can be machined and brazed into housings, creating an exceptional thermal interface and simplifying the overall system complexity which results in higher quality and more repeatable parts. Alle Rechte vorbehalten. Pore size measured as PPI, the linear density of pores per inch (5-40 ppi). Notice, Smithsonian Terms of An analytical model was developed based assuming local thermal non-equilibrium that accounts for the temperature difference between solid and fluid phase. One of the most important features of the RMFs is their extremely high and scalable surface area density (s ) compare to those of brazed or extruded fins and fin pins. Figure 3. The foam manufacturing process preserves the high purity of the material in the RMF.
